Коммуникация, связь, радиоэлектроника и цифровые приборы
Регулировка длин рычагов. Рычажные механизмы состоят из рычагов стержней ползунов соединенных в кинематические пары. Подвижные звенья конструктивно могут быть выполнены в виде рычагов пранок пластин пружин стержней соединяемых между собой высшими нисшими кинематическими парами. Стержневые чаще всего имеют круглое сечение пластинчатые прямоугольное сечение объемных или профильных рычагов может быть любое.
Рычажные механизмы. Классификация. Конструкции. Регулировка длин рычагов.
Рычажные механизмы состоят из рычагов, стержней, ползунов, соединенных в кинематические пары. Предназначены для перредачи и преобразования движений, перемещений, скоростей, силовых воздействий, для выполнения математических операций.
Подвижные звенья конструктивно могут быть выполнены в виде рычагов, пранок, пластин, пружин, стержней, соединяемых между собой высшими (нисшими) кинематическими парами. Объединяющим звеном рычажного узла могут быть корпус, кронштейн, плата, мост.
Виды рычажных механизмов: синусный и тангенсный механизмы.
1. синусный (дает увеличение)2. тангенсный (уменьшение)
Примеры применения:
1-шток 2- коромысло 3- пружина силового замыкания 4- рычаг арретира 5- кнопка 6- контролируемая деталь 7- пятка.
При поступательном перемещении штока 1 коромыслу 2 сообщается поворот относительно оси О, второе плече коромысла снабжено стрелкой, перемещающейся относительно шкалы. Арретир предназначен для отвода штока в момент замены контролируемой детали.
Последовательное соединение 2-х синусных (тангенсных) механизмов.
Позволяет получать линейную функцию перемещения в достаточно широком диапазоне.
Следует соблюдать следующие условия:
Последовательно могут быть соединены два механизма одного типа (2 синусных или 2 тангенсных)
Геометрические размеры влияющие на кинематику для обоих механизмов должны быть одинаковы.
Хотя перемещение звеньев 1 и 2 связаны между собой линейно, зависимость перемещения звеньев 1 и 3 нелинейна.
Поводковые механизмы.
Предназначены для передачи вращения между валами при небольшом диапазоне изменения входного угла.
Изменяя параметры l 1 и l 2, также углю наклона поводков и, изменяя форму поводки, можно получить любую зависимость между входным и выходным углом.
Эти механизмы требуют силового или геометрического замыкания если момент на выходном валу мал или отсутствует. Геометрическое замыкание осуществляется посредствам установки на одном из поводков ползуна щарнирно сочлененного с ползуном на втором поводке. Силовое замыкание достигается установкой на выходном звене спиральной пружины (волоска).
Кривошипно ползунные механизмы.
Предназначены для преобразования вращательного движения кривошипа в возвратно поступательное движение ползуна посредствам ползуна.
1-кривошип 2-шатун 3-ползун.
Различают аксиальный и дезаксиальный кривошипно шатунный механизм (в нем вектор скорости ползуна смещен относительно оси вращения кривошипа на величину е-аксиал).
Характеристикой механизма является зависимость перемещения ползуна от угла поворота кривошипа. На нее влияют радиус кривошипа; длина шатуна; величина аксиала.
В общем случае зависимость не линейна, но при соотношении e / r =0,75 на характеристике имеется линейный участок.
Также механизм имеет мертвые точки при совпадении осей кривошипа и шатуна.
Кулисный механизм.
Применяют для преобразования вращательного движения кривошипа 1 в качательное движение кулисы 2. Ползун 3 (камень) перемещается при этом поступательно.
Кулисные механизмы могут использоваться для преобразования равномерного вращения кривошипа в неравномерное вращательное движение кулисы, если межосевое расстояние e < r .
Конструкции рычажных механизмов.
Рычаги совершающие вращательное, колебательное или переносное движение могут иметь прямолинейную, криволинейную или более сложную пространственную форму.
Разделяют: 1) стержневые 2) пластинчатые 3) объемные 4) профильные.
Стержневые чаще всего имеют круглое сечение, пластинчатые прямоугольное, сечение объемных или профильных рычагов может быть любое.
Различают также: 1) цельные рычаги 2) составные рычаги.
1.Стержневой цельный. 2.Стержневой составной 3.Стержневой пластинчатый 4.Объемный 5.Профильный.
Тип выбирают исходя из требований жесткости, массы, технологичности. Большую жесткость имеют объемные и профильные рычаги (применяются если рычаг находится в сложном напряженном состоянии). Стержневые и пластинчатые применяются в основном для работы при напряжении сжатия, т.е. для восприятия усилия вдоль продольной оси рычага. Необходимо учесть возможность потери продольной устойчивости пычага.
Способы соединения рычагов.
Определяют с учетом типа рычага, диаметра оси, требований к моменту трения и величины зазора в шарнире.
1. Соединение двух цельных стержневых рычагов.
2. Соединение цельного стержневого и пластинчатого рычага.
3. Соединение двух пластинчатых рычагов. и т. д.
Для снижения трения и уменьшения зазоров в шариках применяются шарикоподшипники различных вариантов исполнения.
Регулировку передаточного отношения рычажных механизмов осуществляют чаще всего посредством изменения длины рычагов. Рабочую длину стержневых и пластинчатых рычагов иногда изменяют изгибом рычага на всей длине (определенном участке).
1,2- рычаги 3- кронштейн 4-подвижная ось 5 регулировочный винт 6- сухарь.
Винт 5 вращается относительно оси не перемещаясь в осевом направлении. Сухарь 6 имеет резьбовое отверстие. При вращении винта он перемещается увлекая ось 4. После регулировки производится стопорение осей.
Поводки в поводковых механизмах чаще всего имеют цилиндрическую форму. При диаметре оси поводка больше 1,5 мм возможна его установка по посадке с натягом. При диаметре меньше 1,5 мм, применяют клемовые зажимы, которые соединяют с валом.
1-клема 2- вам 3- поводок 4- фиксирующий винт.
Конструкции рычагов кулисных механизмов.
Кривошип и кулиса могут быть выполнены в виде пластинчатого, объемного или профильного рычагов. При этом палец кривошипа (наиболее нагруженная деталь чаще изготавливают отдельно).
При использовании в качестве кривошипа стержневого рычага палец может быть получен отгибом конца рычага.
Для снижения трения можно установить ролик (или стандартный шарикоподшипник). Такие элементы применяются чаще в силовых механизмах.
1-кривошип 2-ось 3-ролик 4-кольцо 5-стопорное кольцо 6-подшипник качения.
А также другие работы, которые могут Вас заинтересовать |
|||
77336. | ИНТЕРВЬЮ КАК МЕТОД ИССЛЕДОВАНИЯ ЭФФЕКТА ПРИСУТСТВИЯ В СРЕДАХ ВИРТУАЛЬНОЙ РЕАЛЬНОСТИ | 37.66 KB | |
Статья посвящена опыту разработки метода исследования переживания эффекта присутствия в средах виртуальной реальности. Ключевые слова: виртуальная реальность; эффект присутствия. Наша работа посвящена исследованию эффекта присутствия основного фактора во многом определяющего виртуальную реальность и отличающего ее от традиционной объемной компьютерной графики. | |||
77337. | Использование жестовых интерфейсов при взаимодействии с объектами | 151.5 KB | |
Задача разработки трехмерных жестовых интерфейсов связана с задачами удаленного взаимодействия с реальными или виртуальными объектами. Таким образом возникает задача разработки новых удобных для осуществления основной деятельности пользователей... | |||
77338. | К проблеме психологического влияния сети Интернет | 16.5 KB | |
Начало XXI века ознаменовалось значительным ростом аудитории сети Интернет. Вместе с этим растет и время проводимое пользователями в сети появились и продолжают появляться разнообразные сервисы в том числе направленные на общение и взаимодействие между людьми. Однако до сих пор не существует единой точки зрения относительно психологического влияния сети Интернет. | |||
77340. | КОМПИЛЯТОР C89 ДЛЯ ПРОЦЕССОРА MCP 0411100101 | 26 KB | |
Бахтерев ИММ УрО РАН Высокопроизводительные процессоры семейства MCp выпускаемые компанией Мультиклет основаны на оригинальной архитектуре с явным параллелизмом инструкций EPIC Explicitly Prllel Instruction Computing. Особенности кодирования параграфов позволяют выполнять их разным количеством связанных специальным коммутатором клеток функциональных устройств MCp; потенциально это количество может меняться во и время работы процессора. Ещё одной особенностью MCp является то что процессор вносит изменения в память системы как... | |||
77341. | Язык программирования 0xfb.L | 65.5 KB | |
Близится выход С0x новой расширенной версии С которая может стать тем самым инструментом но стандарт С сам по себе очень сложен синтаксис система типов виртуальные методы не все компиляторы поддерживают все возможности поэтому расширение кажется спорным решением. Концепция является результатом развития идей метапрограммирования Lisp Nemerle и сводится к динамическому выстраиванию окружения состоящего из типов переменных и операторов во время компиляции. В процессе компиляции каждое выражение синтаксическая конструкция... | |||
77342. | МАНИПУЛЯТОРЫ ДЛЯ СИСТЕМ НАУЧНОЙ ВИЗУАЛИЗАЦИИ | 244.5 KB | |
И если для средств вывода уже есть такие мощные средства как системы типа Cve стерео очки стерео мониторы и шлемы виртуальной и расширенной реальности то в области средств ввода или манипуляторов таких решений очень мало и не имеют большого распространения. Нами была поставлена задача разработать интерфейс для работы с виртуальными объектами в котором бы учитывались достоинства и недостатки уже существующих манипуляторов и который был бы максимально прост и естественен в использовании. Обзор существующих решений Был проведён критический... | |||
77343. | Манипуляция объектами в системах компьютерной визуализации | 38.5 KB | |
Серьезной задачей в системах визуализации является обеспечение различных действий с визуальными объектами при работе с трехмерной графикой. Как правило, при реализации методов непосредственного манипулирования с визуальными объектами все операции проводятся в основном окне вывода | |||
ВИДЫ ДВИЖЕНИЙ И ПЕРЕДАТОЧНЫЕ МЕХАНИЗМЫ
Вращательное движение
Вращательное движение в машинах передается при помощи фрикционной, зубчатой, ременной, цепной и червячной передач. Будем условно называть пару, осуществляющую вращательное движение, колесами. Колесо, от которого передается вращение, принято называть ведущим, а колесо, получающее движение, - ведомым.
Всякое вращательное движение измеряется в числах оборотов в минуту. Зная число оборотов в минуту ведущего колеса, мы можем определить число оборотов ведомого колеса (рис. 6).
Число оборотов ведомого колеса зависит от соотношения диаметров соединенных колес. Если диаметры обоих колес будут одинаковы, то и колеса будут крутиться с одинаковой скоростью. Если диаметр ведомого колеса будет больше ведущего, то ведомое колесо станет крутиться медленнее, и наоборот, если его диаметр будет меньше, оно будет делать больше оборотов.
Многие, наверное, замечали, что маленькая звездочка у цепной велосипедной передачи крутится быстрее, чем большая, а большая шестерня, с барабаном для каната у лебедки, делает оборотов меньше, чем ее ведущая меньшая пара.
Известны простые правила: 1) число оборотов ведомого колеса во столько раз меньше числа оборотов ведущего, во сколько раз его диаметр больше диаметра ведущего колеса; 2) число оборотов ведомого колеса во столько раз больше числа оборотов ведущего, во сколько раз его диаметр меньше диаметра ведущего колеса.
В технике при конструировании машин часто приходится определять диаметры колес и число их оборотов. Эти расчеты можно делать на основе простых арифметических пропорций. Например, если мы условно обозначим диаметр ведущего колеса через Д-t, диаметр ведомого через Д2, число оборотов ведущего колеса через пх, число оборотов ведомого колеса через щ, то все эти величины выражаются простым соотношением
Если нам известны три величины, то, подставив их в формулу, мы легко найдем четвертую, неизвестную величину.
В практике работы технических кружков часто приходится употреблять выражения: «передаточное число» и «передаточное отношение».
Что же означают эти названия?
Передаточным числом называют отношение числа оборотов ведущего колеса (вала) к числу оборотов ведомого, а передаточным отношением - отношение между числами оборотов колес независимо от того, какое из них ведущее.
Рассмотрим некоторые виды вращательного движения, которые нашли широкое применение в моделях юных техников.
Фрикционная передача
При фрикционной передаче вращение от одного колеса к другому передается при помощи силы трения. Оба колеса прижимаются друг к другу с некоторой силой и вследствие возникающего между ними трения вращают одно другое.
Фрикционные передачи широко применяются в машинах. Недостаток фрикционной передачи: большая сила, давящая на колеса, вызывающая дополнительное трение в машине, а следовательно, требующая и дополнительную силу для вращения.
Кроме того, колеса при вращении, как бы они ни были прижаты друг к другу, дают проскальзывание. Поэтому там, где требуется точное соотношение чисел оборотов колес, фрикционная передача себя не оправдывает.
В моделях фрикционная передача может быть широко использована. Особенно приемлемы для моделей передачи цилиндрическая и лобовая (рис. 7). Колеса для передач можно делать деревянные и металлические. Оси колес делают из проволоки или вытачивают на токарном станке.
Для лучшего сцепления рабочие поверхности колес следует «обшить» слоем мягкой резины толщиной в 2-3 мм. Резину можно или прибить мелкими гвоздиками, или приклеить клеем БФ-2.
В моделях удобно применять комбинированную фрикционную передачу, то-есть одно из колес делается с резиновой обшивкой, а на ведущем набивают проволочные шпильки. Шпильки лучше набивать в два-три ряда в шахматном порядке, без строгого соблюдения расстояния между ними. Шпильки можно делать из гвоздей, только без шляпок. Такая комбинированная передача работает в модели жатки-самосброски: она передает вращение грабельному устройству.
В зубчатых передачах вращение от одного колеса к другому передается при помощи зубцов. Зубчатые колеса работают намного легче фрикционных. Объясняется это тем, что здесь нажима колеса на колесо совсем не требуется.
Для правильного зацепления и легкой работы колес профиль зубца делают по определенной кривой, называемой эвольвентой.
Диаметр начальной окружности является основным расчетным диаметром зубчатых колес. Расстояние, взятое по начальной окружности между осями соседних зубцов, между осями впадин или от начала одного зубца до начала другого, называется шагом зацепления (рис. 8,6). Разумеется, что шаги у зацепляющихся шестерен должны быть равны.
Передаточное число в зубчатых колесах может выражаться и через число зубцов,то-есть j = |2-> где г2-число зубцов ведомого колеса, zx - число зубцов ведущего колеса.
Есть в шестернях еще одна очень важная величина, которую именуют модулем. Модулем называют отношение шага к величине Пи (3,14) или отношение диаметра начальной окружности к числу зубцов на колесе. Модуль, шаг и другие величины шестерен измеряются в миллиметрах. Колеса с одинаковым модулем, с любым количеством зубцов дают нормальное зацепление.
Модули зубчатых колес берутся не произвольно. Величины их стандартизированы.
Передаточное число шестеренчатой передачи берется обычно в определенных пределах. Оно колеблется до 1: 10. При увеличении передаточного числа одна из шестерен делается очень большой, механизм получается громоздким.
Но иногда бывает нужно получить очень большое передаточное число, которое одной парой шестерен создать трудно. В этом случае ставится несколько пар и передаточное число распределяется между ними.
Механизм, служащий для повышения или понижения скорости вращения, называется редуктором. Редукторы с большим передаточным числом обычно служат для снижения числа оборотов. Если такой редуктор использовать для увеличения числа оборотов, то получаются большие сопротивления и редуктор очень трудно вращать.
Иногда в передачах малую шестерню требуется сделать особенно уменьшенной, например в часах, в приборах.
В этих случаях шестерню с валом делают из одного куска. Такую цельную шестерню принято называть трибком (трибок).
За последнее время очень часто в машинах применяют цилиндрические шестерни, у которых зубец идет не по оси вращения, а под некоторым углом (рис. 8,г). Такие шестерни работают на больших скоростях очень плавно, и зубцы их выносят большую нагрузку.
Колеса с косыми зубцами носят название косозубых цилиндрических колес.
Еще более плавный ход при большой прочности зубцов дают так называемые шевронные колеса (рис. 8,(3). Зубцы у этих колес скошены в обе стороны, расположены «в елочку». Преимущество шевронных колес состоит в том, что их можно применять с малым числом зубцов.
Шестеренчатая передача применяется не только с параллельными валами, когда используются так называемые цилиндрические шестерни, но и тогда, когда валы идут под любым углом. Такая передача под углом называется конической зубчатой передачей, а шестерни - коническими (рис. 8,ж).
Если в цилиндрических зубчатых передачах мы могли сцепить колеса любых размеров (только с одинаковым модулем), то в конических шестернях этого сделать нельзя, так как в этом случае может не совпасть конусность шестерен.
Конические шестерни, так же как и цилиндрические, бывают со спиральным косым зубцом (рис. 8,з). Такие шестерни обычно применяются в автомобилях (для плавности работы). В зубчатых передачах можно применить шестерни с рейкой (рис. 9). Реечные передачи применяются и в моделях.
Для периодического вращения может применяться шестеренчатая пара, у которой ведущая шестерня имеет неполное число зубцов.
Ведущие шестерни встречаются и с одним зубцом. Такие передачи очень часто применяются в счетных механизмах. Ведущая шестерня имеет один зубец, а ведомая - десять (рис. 10,а), и, таким образом, за один оборот ведущей шестерни ведомая повернется всего на одну десятую оборота. Чтобы повернуть ведомую шестерню на один оборот, ведущая должна сделать десять оборотов.
К разобранному типу передач можно отнести и так называемое мальтийское зацепление, или мальтийский крест (рис. 10,6).
Механизм мальтийского креста применяется в автоматах, текстильных машинах и в киноаппаратах, где он служит для периодической подачи ленты. Для моделей мальтийский крест легко вырезать из листового материала. Ведущий вал можно загнуть из проволоки, в виде кривошипа. Хорошо сделать ведущий вал с планшайбой, с поводком-гвоздиком. Прорези креста можно оформить шпильками, забитыми в деревянный диск.
Применение зубчатых колес в моделях.
Шестерни в моделях применяются довольно часто. Обычно стараются применять готовые шестерни от разных машин и механизмов. Но иногда их приходится делать самим.
Изготовление шестерен является довольно кропотливой работой и требует от кружковца большого умения. Мы опишем пять способов изготовления шестерен: с вывернутыми, шпилечными, пластинчатыми, выгнутыми и вырезанными зубцами. Следует заметить, что при изготовлении шестерен не соблюдается ни модуль, ни настоящая форма зубца.
Шестерни с вывернутыми зубцами (рис. 12) (таблица 1, см. приложения) изготовляются из листового материала толщиной 0,5-- 1 мм. Лучше всего их изготовлять из алюминия, цинка, латуни и меди.
Согласно выбранному диаметру чертят, а затем вырезают круг. После этого круг по окружности делят по транспортиру на число зубцов. Например, шестерня должна быть с 24 зубцами, угол деления для каждого
360° зубца будет равен 15°, то-есть ~гг = 15 .
Если шестерня слишком мала или велика для накладывания на нее транспортира, деления можно наносить на листе бумаги, затем переводить на шестерню.
После разметки зубцы надрезаются на нужную глубину и вывертываются плоскогубцами перпендикулярно плоскости.
Для удобства посадки шестерни на вал или на ось к ней прикрепляется втулочка. Металлическую втулочку можно припаять, а деревянную прибить гвоздиками, иногда втулку приклеивают специальным клеем.
Основной частью шестерни со шпилечными зубцами (таблицы 5 и 6) является деревянное колесо. В него набиваются проволочные шпильки - зубцы, с помощью которых передается вращение.
Шестерни со шпилечными зубцами бывают двух видов. У одних зубцы расположены по окружности, у других - по торцу (сбоку). Для передачи вращения при параллельных валах берется по одной шестерне с боковыми и с окружными зубцами. При этом ведущая шестерня должна быть с окружными зубцами, а ведомая - с боковыми. Для передачи вращения при валах, расположенных.под углом, применяются одинаковые шестерни: или с боковыми, или с торцовыми зубцами. Диаметр зубцов берется от 1 до 2,5 мм. Тонкие зубцы можно делать из гвоздей. Гвозди забиваются в колесо, и головки их откусываются кусачками. Толстые зубцы лучше делать из мягкой алюминиевой или медной проволоки (диаметр применяемой проволоки не зависит от размера шестерни).
Перед забивкой зубцов на колесе обязательно нужно сделать разметку. У шестерен с боковым расположением зубцов разметка делается так же, как и у шестерен с вывернутыми зубцами: проводится окружность и на ней делается градусная разбивка. У шестерен с зубцами, расположенными по окружности, разметка делается иначе. По окружности колеса огибается полоска бумаги. Ее концы накладывают друг на друга и разрезают острым ножом. Затем полоска снимается и размечается на равные части по количеству зубцов. После этого полоска снова накладывается на колесо и через намеченные места делаются наколы для зубцов. Для разметки вместо простой бумаги хорошо взять миллиметровую.
При толстых зубцах посадочные места следует надсверливать, иначе можно расколоть колесо.
Боковые зубцы, идущие вдоль волокон дерева, можно забивать без сверления отверстий.
У шестерен с пластинчатыми зубцами (приложение 29) вместо шпилек зубцы делаются из жести. Толщина пластин берется в пределах от 0,5 до 1 мм. Пластины или забиваются в колесо, или делаются в виде шипов (по два зубца), прикрепляются к колесу гвоздями или шурупами. Зубцы должны быть широкими, особенно у шестерен, в которых зубцы крепятся шурупами.
Пластинки для зубцов можно подобрать готовые. Особенно пригодны для пластинок обрезки гвоздей после ковки лошадей.
Пластинчатые зубцы можно набивать и сбоку колеса, как шпильки. Такой шестерней в сцеплении со шпилечной можно передавать вращение под углом.
Шестерни с пластинчатыми зубцами обычно применяются для передачи при параллельных валах.
Изготовлять шестерни всех типов (с вывернутыми зубцами, со шпилечными, с пластинчатыми) нужно очень тщательно. Колеса лучше всего делать точеными, расположив волокна вдоль оси вращения.
Зубцы после посадки нужно старательно выверить. Выверку легко производить отгибанием зубцов плоскогубцами в ту или другую сторону. Разница в шаге допускается не более 0,5-1 мм. Чем точнее шестерня изготовлена, тем более плавно она будет работать. Концы зубцов должны быть тщательно обработаны. У толстых зубцов (от 1,5 мм) концы, что идут к соседним зубцам, спиливаются клином и притупляются.
Для надежного зацепления при угловой передаче зубцы следует набивать как можно ближе к краю или отгибать, как показано на рисунке 12,г.
Чтобы высота зубцов была одинаковой, зубцы необходимо проверять простым шаблоном (рис. 12, к).
Устанавливая шестерни на место, зацепление надо хорошенько отрегулировать, удаляя или сближая оси шестерен.
Шестерни с выгнутыми зубцами выгибаются волнообразно из жестяной полоски толщиной не более 0,4 мм и шириной 6-8 мм. После этого полоска сгибается по наружному размеру шестерни и концы ее соединяются пайкой.
Такие колеса часто применяются в детском «Конструкторе». Зацепление этих колес довольно хорошее, но они трудны для изготовления.
Хорошие шестерни с гнутыми зубцами можно изготовлять при помощи приспособления, показанного на рисунке 12,и.
Некоторые шестерни можно выпиливать из толстого металла.
Большие деревянные шестерни делают по типу мельничных.
Число оборотов шестерен в моделях можно легко рассчитать. При расчете берется во внимание число зубцов, а не диаметр шестерни.
Ременная передача
Ременная передача (рис. 13), как и шестеренчатая, весьма часто встречается в машинах. Она применяется там, где валы удалены друг от друга на большое расстояние и шестеренчатую передачу применить нельзя.
Ремень, натянутый на шкивы, охватывает какую-то их часть. Эта облегающая часть (дуга) носит название угла обхвата. Чем больше будет угол обхвата, тем лучше образуется сцепление, лучше и надежнее будет вращение шкивов. При малом угле обхвата может получиться так, что ремень на малом шкиве станет проскальзывать, вращение будет передаваться плохо или совсем не будет.
Угол обхвата зависит от соотношения размеров шкивов и их расстояния друг от друга. На рисунках \2>,а,б показано, как меняются углы обхвата от указанных причин.
Когда требуется увеличить угол обхвата, у передачи ставят нажимной шкив-ролик в зависимости от расположения валов и ремня ременная передача бывает разных видов.
Открытая передача (рис. 13,г). Оба шкива при такой передаче вращаются в одну сторону.
Перекрестная передача (рис. 13,5). Такую передачу применяют, когда требуется изменить вращение ведомого шкива. Шкивы вращаются навстречу друг другу.
Полуперекрестная передача (рис. 13,е) применяется, когда валы лежат не параллельно, а под углом.
Угловая передача (рис. 13,ж) образуется, когда валы идут под углом, но лежат как бы в одной плоскости. При этой передаче для получения надлежащего направления ремня обязательно устанавливают ролики.
Спаренная передача (рис. 13,з). При этой передаче с одного ведущего шкива могут итти ремни на несколько ведомых шкивов.
Кроме перечисленных передач, бывает еще и ступенчатая передача (рис. 13,и). Она применяется тогда, когда требуется изменять число оборотов ведомого вала.
Оба шкива в этой передаче делаются ступенчатыми. Переставляя ремень на ту или иную пару ступеней, меняют число оборотов ведомого вала. При этом длина ремня остается неизменной.
По своему профилю ремни бывают плоские, круглые и трапецеидальные (рис. 13, к, л, м).
В мелких машинах и разного рода приборах вместо круглого шнурового ремня употребляется ремень, сделанный из тонкой проволоки в виде пружины. Такое устройство ремня облегчает работу шкивов. Толщина проволоки - 0,2 - 0,3 мм, а диаметр ремня (пружины) - 4-6 мм.
На концах пружины отгибаются крючки, которыми она сцепляется.
Передаточное число ременных передач берется в пределах 1:4; 1:5 и только в исключительном случае --до 1:8.
Расчет ременной передачи производится по формулам 1 и 2.
При расчете учитывается скольжение ремня по шкивам. Это проскальзывание выражается в пределах 2-3%. Чтобы получить нужные обороты, диаметр ведомого шкива уменьшают в этих же пределах.
Ременные передачи успешно применяют в моделях. Особенно хорошо применять легкие передачи с пружинным и шнуровым круглым ремнем.
Кроме шнура и бечевки, ремнем может служить и резиновая тесьма. Плоские ремни должны быть тонкими и мягкими. Шкивы следует вытачивать из дерева или легких металлов.
Кривошипно-шатунные механизмы
Кривошипно-шатунные механизмы служат для преобразования вращательного движения в возвратно-поступательное и наоборот.
Основными деталями кривошипно-шатунного механизма являются: кривошипный вал, шатун и ползун, связанные между собой шарнирно (рис. 14,а). Длину хода ползуна можно получить любую, зависит она от длины кривошипа (радиуса).
В кривошипно-шатунном механизме вместо кривошипного вала часто применяют коленчатый вал. От этого сущность действия механизма не меняется.
Коленчатый вал может быть как с одним коленом, так и с несколькими (рис. 14, б, в),
Видоизменением кривошипно-шатунного механизма может быть также эксцентриковый механизм (рис. 14,г). У эксцентрикового механизма нет ни кривошипа, ни колен. Вместо них на вал насажен диск. Насажен же он не по центру, а смещено, то есть эксцентрично, отсюда и название этого механизма - эксцентриковый.
В некоторых кривошипно-шатунных механизмах приходится менять й длину хода ползуна. У кривошипного вала это делается обычно так. Вместо цельного выгнутого кривошипа на конец вала насаживается диск (план-шайба). Шип (поводок, на что надевается шатун) вставляется в прорез, сделанный по радиусу план-шайбы. Перемещая шип по прорезу, то-есть удаляя его от центра или приближая к нему, мы меняем размер хода ползуна.
Ход ползуна в кривошипно-шатунных механизмах совершается неравномерно. В местах «мертвого хода» он самый медленный.
Кривошипно-шатунные механизмы применяются в двигателях, прессах, насосах, во многих сельскохозяйственных и других- машинах.
Кривошипно-шатунные механизмы применяются и в моделях. Один из таких механизмов с коленчатым валом применен у моделей жатки-самосброски, сенокосилки. Он приводит в возвратно-поступательное движение ножи.
Эксцентриковый механизм для моделей сделать нетрудно (рис. 15).
Детали для механизма могут быть сделаны как из дерева, так и из жести, проволоки и т. п.
Можно сделать механизм и Q переменным эксцентриком.
Кулисные механизмы
Возвратно-поступательное движение в кривошипных механизмах можно передавать и без шатуна. В ползушке, которая в данном случае называется кулисой, делается прорез поперек движения кулисы (рис. 16). В этот прорез вставляется палец кривошипа. При вращении вала кривошип, двигаясь влево и вправо, водит за собой и кулису.
Устройство кулисного механизма с эксцентриком показано на рисунке 16,а,б,в.
Вместо кулисы можно применить стержень, заключенный в направляющую втулку. Для прилегания к диску эксцентрика стержень снабжается нажимной пружиной. Если стержень работает вертикально, его прилегание иногда осуществляется собственным весом.
Для лучшего движения по диску на конце стержня устанавливается ролик.
Иногда в машинах возвратно-поступательное движение передается с переменными ходами, то-есть в одну сторону ползун движется с одной скоростью, а в обратную - с другой.
Такой механизм применен в поперечно-строгальном станке.
Храповые механизмы
Кроме непрерывного вращательного движения, в машинах очень часто применяется прерывистое вращательное движение. Такое движение осуществляется при помощи так называемого храпового механизма (рис. 17).
Основными частями храпового механизма являются: храповик (диск с зубцами), рычаг и собачка. Зубцы храповика имеют особую форму. Одна сторона у них сделана пологой, а другая отвесной или несколько подвнутренной.
Храповик насажен на вал неподвижно. Рычаг же, сидящий рядом с храповиком, может свободно качаться. На рычаге имеется собачка, которая одним концом лежит на храповике.
С помощью шатуна или тяги от того или иного ведущего механизма рычаг приходит в карательное движение, При отклонении рычага влево собачка скользит свободно по пологому склону зубцов, не поворачивая храповик. При отходе вправо собачка упирается в уступ зубца и поворачивает храповик на некоторый угол. Так, непрерывно качаясь в ту и другую сторону, рычаг с собачкой приводит храповик с валом в периодическое вращательное движение.
Для надежного прилегания собачки к храповику собачка снабжается нажимной пружиной.
Но бывает и другое назначение храпового механизма: для предохранения вала с храповиком от проворачивания. Так, у лебедки при подъеме груза храповик с собачкой не дают барабану провертываться обратно.
Иногда нужно получить вращение храповика не только в одну сторону, но и в другую. В этом случае зубцы у храповика делают прямоугольными, а собачку - перекидной (рис. 17,6). Перекинув собачку вправо или влево, можно изменить и вращение храповика.
Число зубцов на храповике зависит от требуемого угла поворота. На какую часть окружности поворачивается храповик, столько делают и зубцов. Например, если на 60° - одну шестую долю окружности, то берут 6 зубцов; на 30° - одну двенадцатую долю - делают 12 зубцов и т. д.
Меньше шести зубцов на храповике обычно не бывает.
Модели храповых механизмов легко сделать из листового металла. Храповик должен быть небольшим. Большой храповик потребует увеличения размаха рычага и большого хода кривошипа, качающего рычаг.
Высоту зубца храповика следует брать в пределах 0,35-0,4 от шага. Профиль зубца делают остроугольным, пологую сторону зубца - прямой, но ее можно и очерчивать по радиусу. Рычагов лучше брать два, помещая их по обеим сторонам храповика. При двух рычагах собачка и поводок от кривошипа встанут между ними и уменьшат перекос при работе. Нажим собачки можно осуществлять не только пружиной, но и резиной. Конец собачки следует хорошо скашивать, чтобы она надежнее упиралась в зубец.
Модели храповых механизмов можно делать и из дерева.
Кулачковые механизмы
Кулачковые механизмы (рис. 18) служат для преобразования вращательного движения (кулачка) в возвратно-поступательное или другой, заданный вид движения. Механизм состоит из кулачка - криволинейного диска, насаженного на вал, и стержня, который одним концом опирается на криволинейную поверхность диска.
Стержень вставлен в направляющую втулку.
Для лучшего прилегания к кулачку стержень снабжается нажимной пружиной. Чтобы стержень легко скользил по кулачку, на его конце устанавливается ролик.
Но бывают дисковые кулачки другой конструкции. Тогда ролик скользит не по контуру диска, а по криволинейному пазу, вынутому сбоку диска (рис. 18,6). В этом случае нажимной пружины не требуется. Движение ролика со стержнем в сторону осуществляется самим пазом.
Кроме рассмотренных нами плоских кулачков (рис. 18,а), можно встретить кулачки барабанного типа (рис. 18,в). Такие кулачки представляют собой цилиндр с криволинейным пазом по окружности. В пазу установлен ролик со стержнем. Кулачок, вращаясь, водит криволинейным пазом ролик и этим сообщает стержню нужное движение.
Цилиндрические кулачки бывают не только с пазом, но и односторонние - с торцовым профилем. В этом случае нажим ролика к профилю кулачка производится пружиной.
В кулачковых механизмах вместо стержня очень часто применяются качающиеся рычаги (рис. 1Ь,в). Такие рычаги позволяют менять длину хода и его направление.
Длину хода стержня или рычага кулачкового механизма можно легко рассчитать. Она будет равна разнице между малым радиусом кулачка и большим.
Например, если большой радиус равен 30 мм, а малый 15, то ход будет 30-15 = = 15 мм.
В механизме с цилиндрическим кулачком длина хода равняется величине смещения паза вдоль оси цилиндра.
Благодаря тому, что кулачковые механизмы дают возможность получить разнообразнейшие движения, их часто применяют во многих машинах. У двигателей внутреннего сгорания кулачковый механизм приводит в действие систему зажигания.
Равномерное возвратно-поступательное движение в машинах достигается одним из характерных кулачков, который носит название сердцевидного. При помощи такого кулачка происходит равномерная намотка челночной катушки у швейной машины.
Для моделей кулачковые механизмы сделать нетрудно. Плоские кулачки легко выпилить из дерева или из толстого алюминия, латуни, меди. Ролики хорошо выточить на токарном станке.
Плоский кулачок с боковым пазом можно сделать так, как показано на рисунке 18,5.
Цилиндрические (пространственные) кулачки для облегчения изготовления паза лучше делать составными. На торцах" двух отдельных цилиндров вырезают требуемый профиль. После этого цилиндры надеваются на вал и между их профильными торцами образуется нужный паз. Упрощенный тип открытого цилиндрического кулачка, может быть получен от косой посадки диска на ось.
Рычаги
Рычаг -простейшее механическое устройство, представляющее собой твёрдое тело (перекладину), вращающееся вокруг точки опоры. Стороны перекладины по бокам от точки опоры называются плечами рычага.
Рычаг используется для получения большего усилия на коротком плече с помощью меньшего усилия на длинном плече (или для получения большего перемещения на длинном плече с помощью меньшего перемещения на коротком плече). Сделав плечо рычага достаточно длинным, теоретически, можно развить любое усилие.
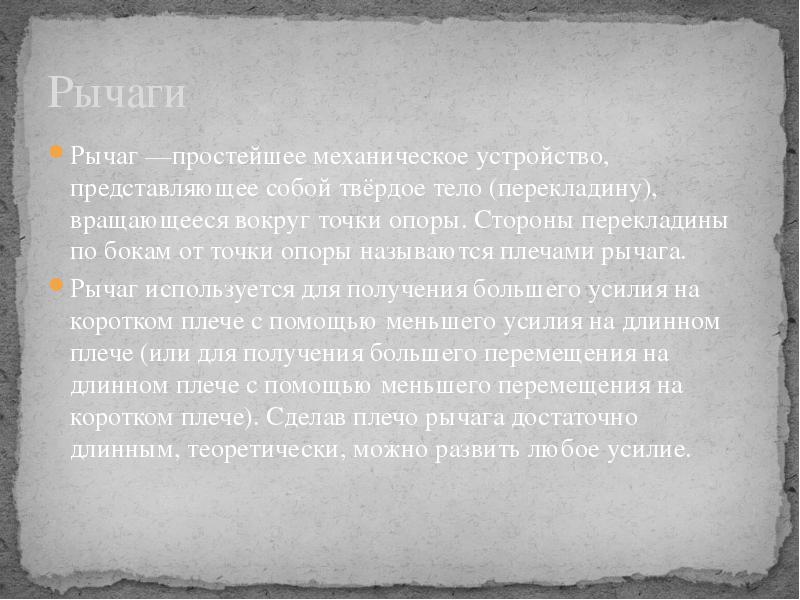
Рычаг 1-ого рода
Различают рычаги 1 рода, в которых точка опоры располагается между точками приложения сил.
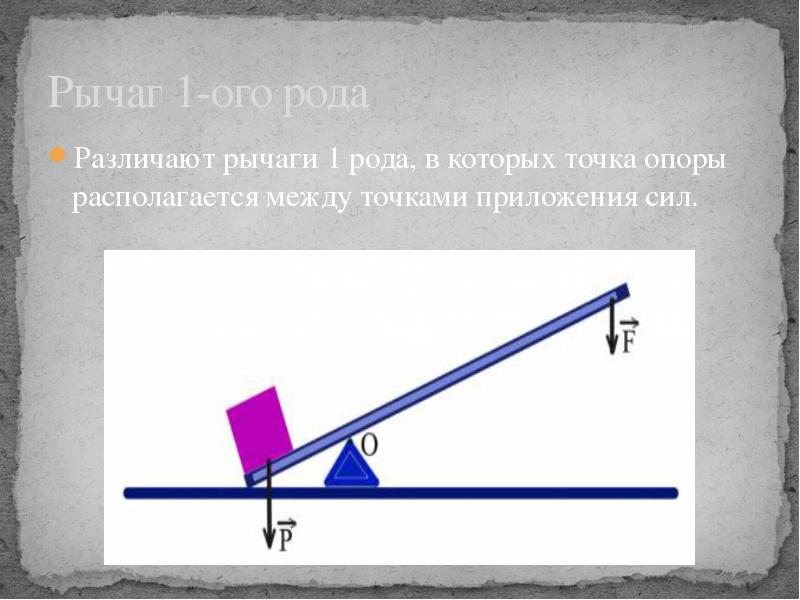
Рычаг 2-ого рода
Рычаги 2 рода, в которых точки приложения сил располагаются по одну сторону от опоры.
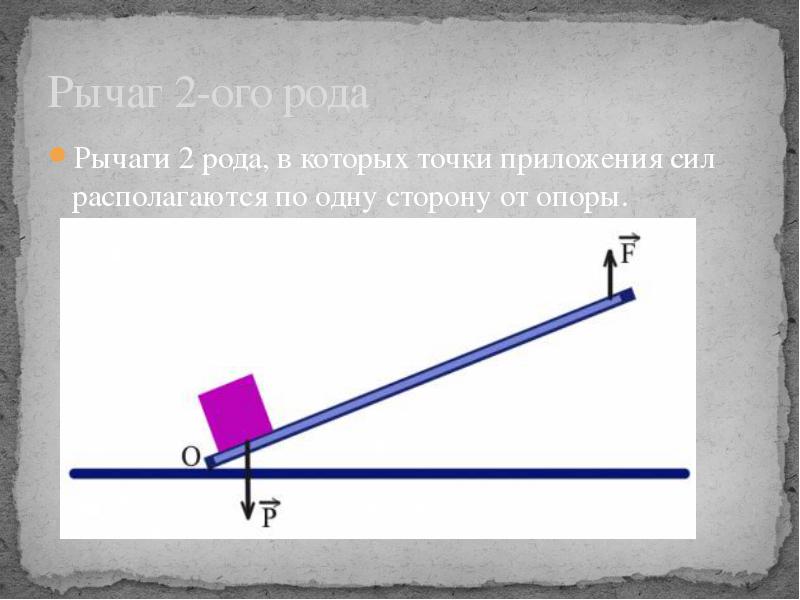
Ремённые передачи
Ремённая передача - это передача механической энергии при помощи гибкого элемента (ремня) за счёт сил трения или сил зацепления (зубчатые ремни). Может иметь как постоянное, так и переменное передаточное число (вариатор), валы которого могут быть с параллельными, пересекающимися и со скрещивающимися осями.
Ремённые передачи бывают прямые и обратные.
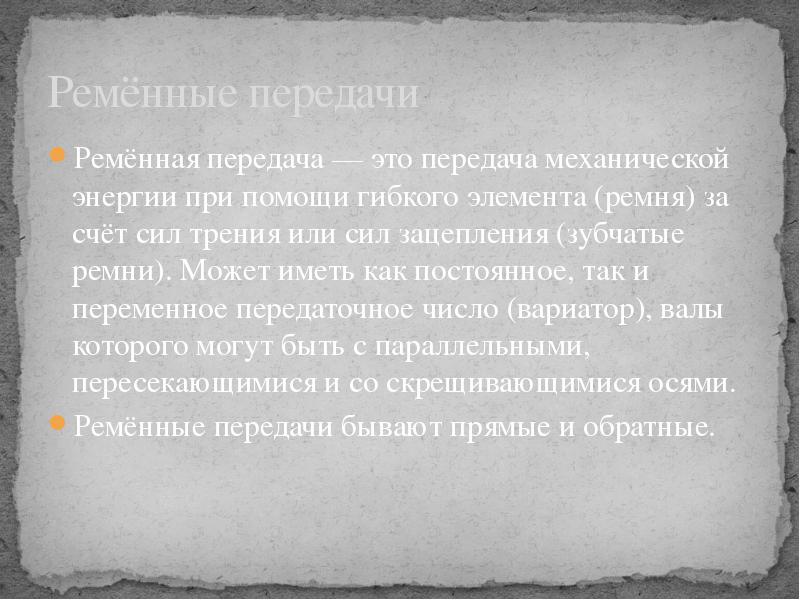
Прямая ременная передача
Прямая ременная передача, при которой колёса совершают вращательное движение одинаково.
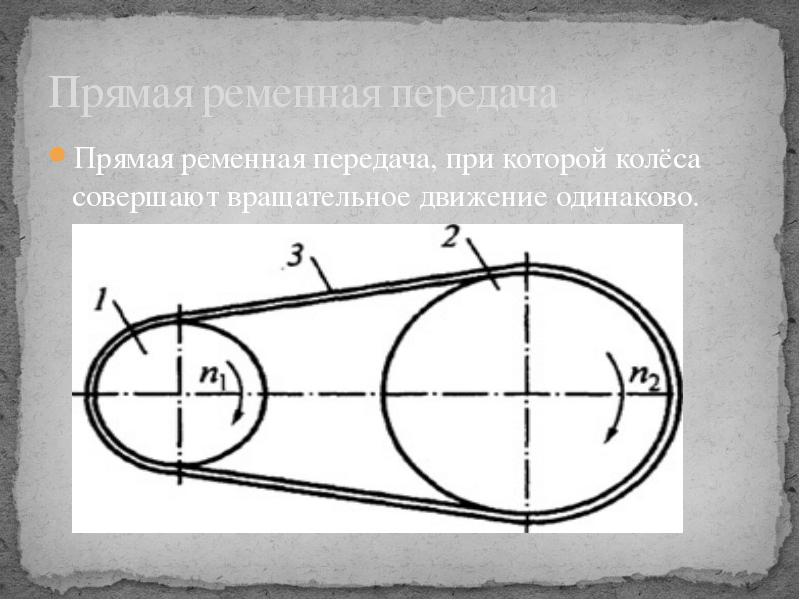
Обратная ременная передача
Обратная ременная передача, при которой колёса совершают вращательное движение по-разному.
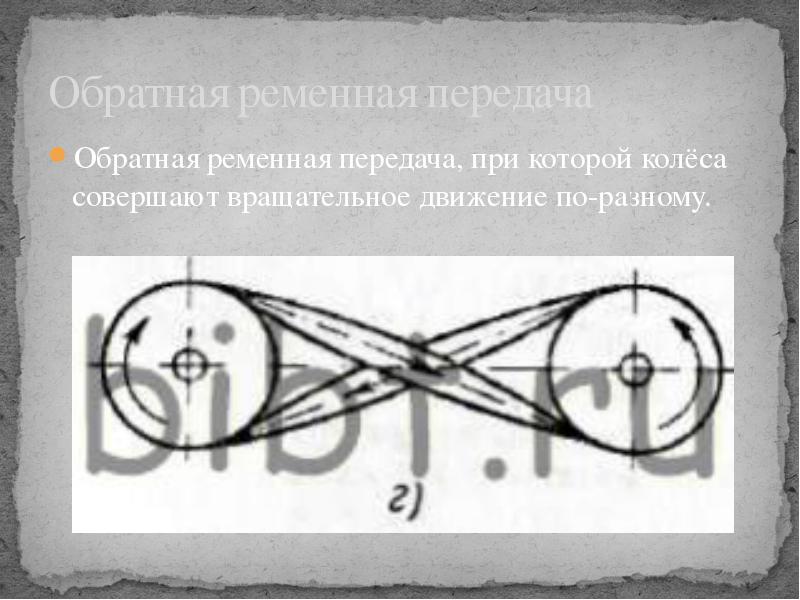
Зубчатая передача
Зубчатая передача - это механизм или часть механизма механической передачи, в состав которого входят зубчатые колёса.
При вращательном движении усилие от одного элемента к другому передаётся с помощью зубьев. Зубчатое колесо передачи с меньшим числом зубьев называется шестернёй, второе колесо с большим числом зубьев называется колесом. Пара зубчатых колёс имеющих одинаковое число зубьев - в этом случае ведущее зубчатое колесо называется шестернёй, а ведомое - колесом.
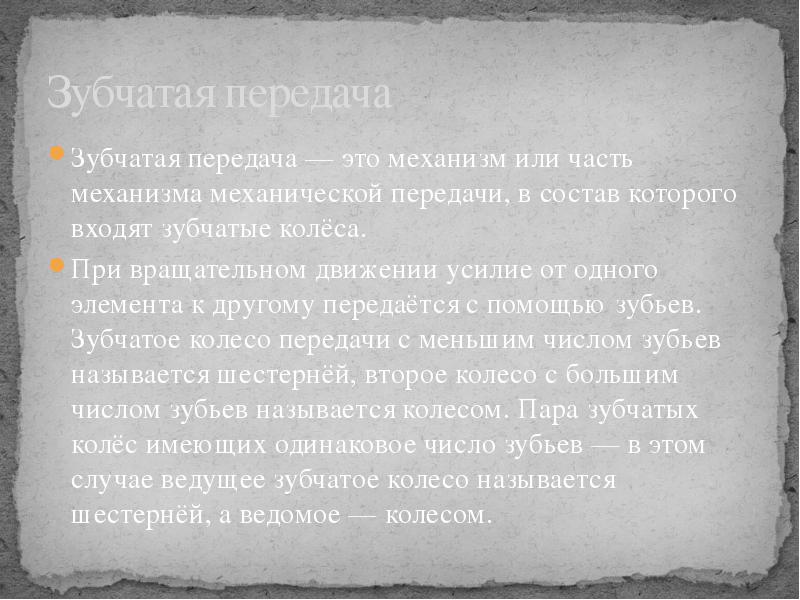
Пантограф
Пантограф - прибор, служащий для перечерчивания планов, карт и т. п. в другом, обычно более мелком масштабе. Пантографы изготовляют различных размеров и разных конструкций (подвесные, на колёсиках и др.). Позволяют одну из вершин двигать по прямой линии.
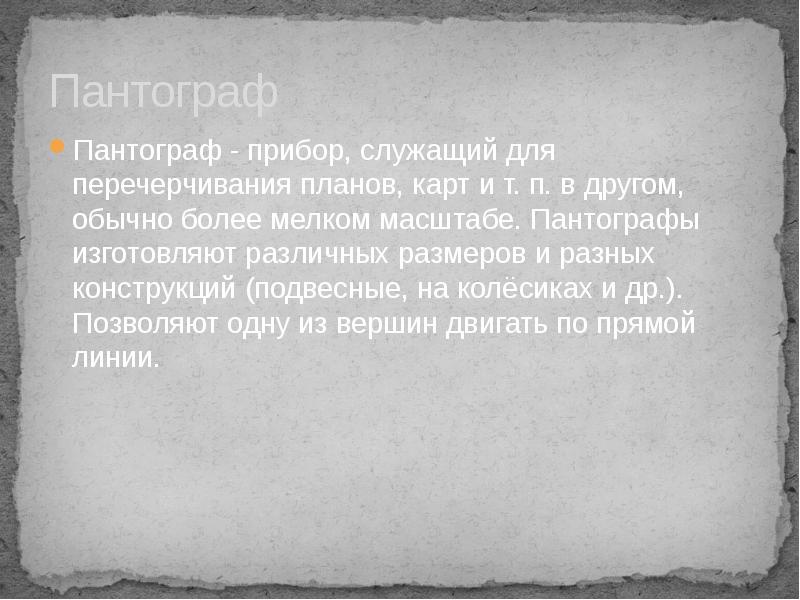
Цилиндрическая зубчатая передача
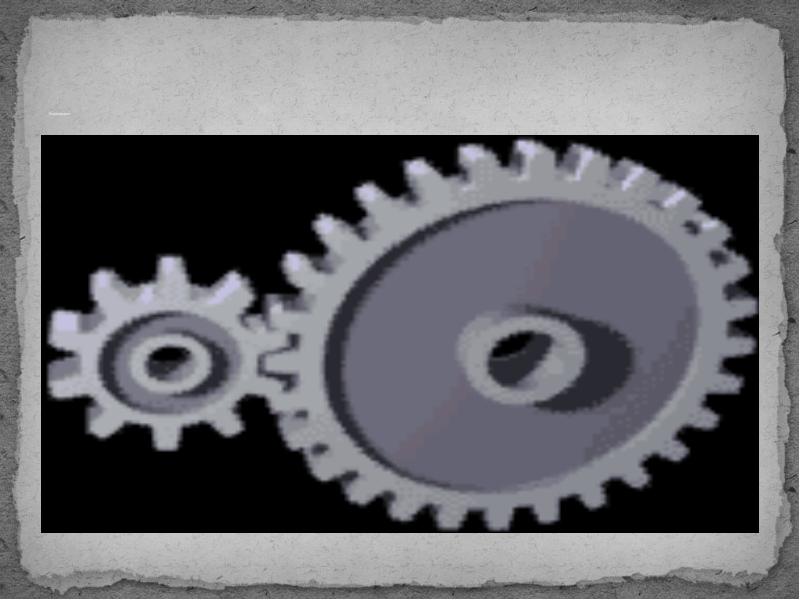
Коническая зубчатая передача
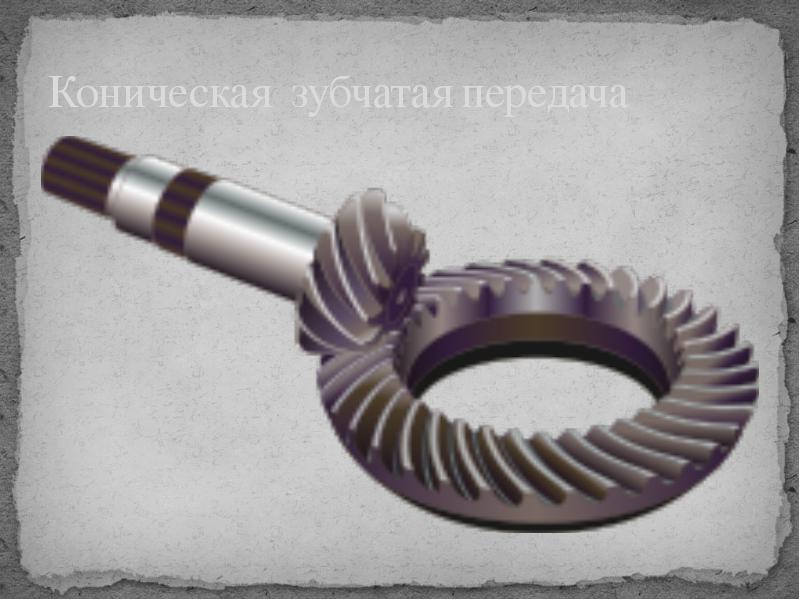
Корончатая шестерня
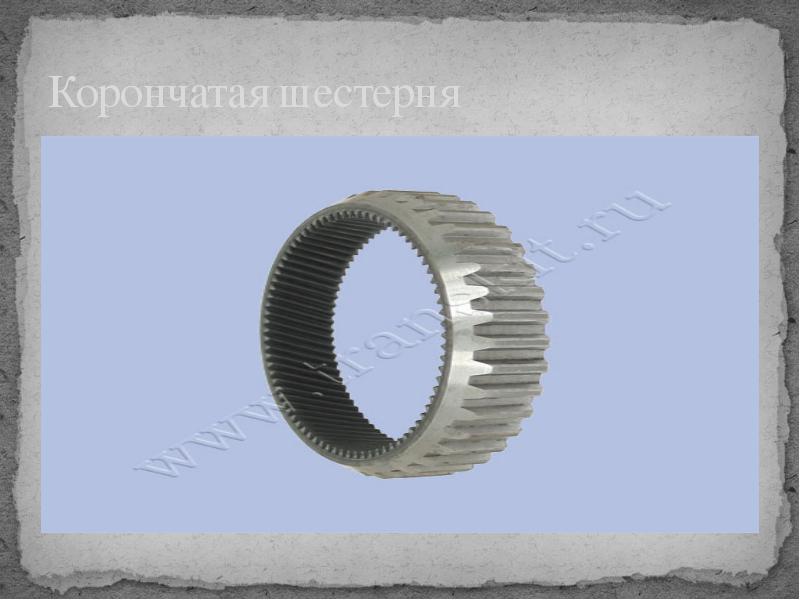
Колесо
Колесо - круглый (как правило), свободно вращающийся или закреплённый на оси диск, позволяющий поставленному на него телу катиться, а не скользить. Колесо повсеместно используется в различных механизмах и инструментах. Широко применяется для транспортировки грузов.
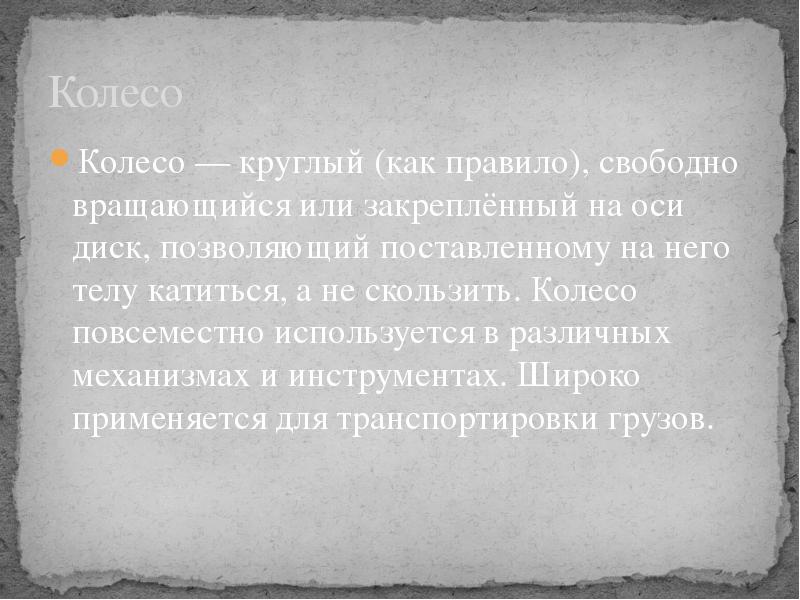
Изображение колеса
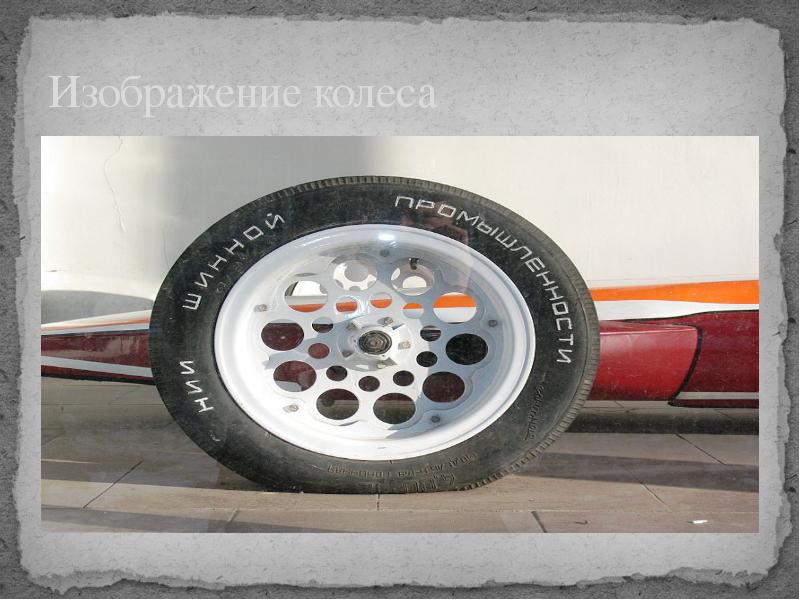
Кулачковый механизм
Кулачковый механизм - механизм, образующий высшую кинематическую пару, имеющий подвижное звено, совершающее вращательное движение, - кулак (кулачок), с поверхностью переменной кривизны или имеющей форму эксцентрика, взаимодействующей с другим подвижным звеном - толкателем, если подвижное звено совершает прямолинейное движение, или коромыслом, если подвижное звено совершает качание. Кулак, совершающий прямолинейное движение, называется копиром.
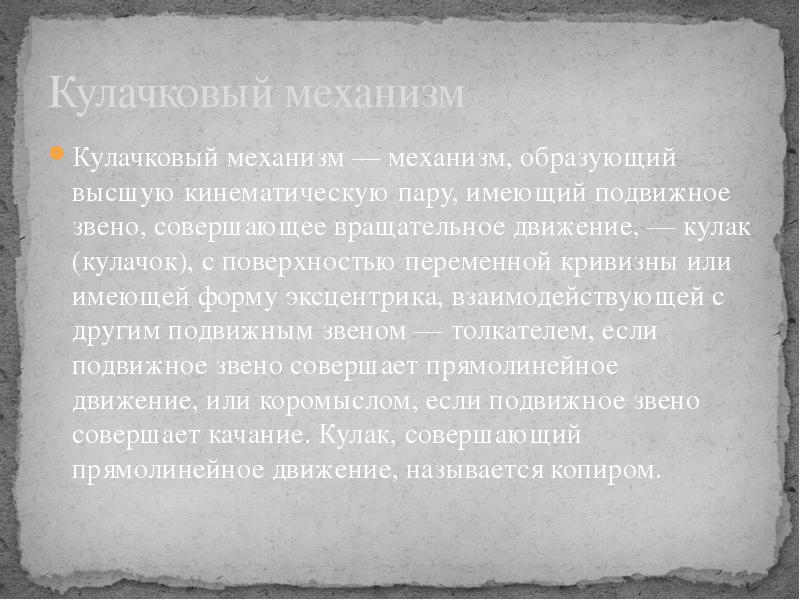
Изображение кулачкового механизма
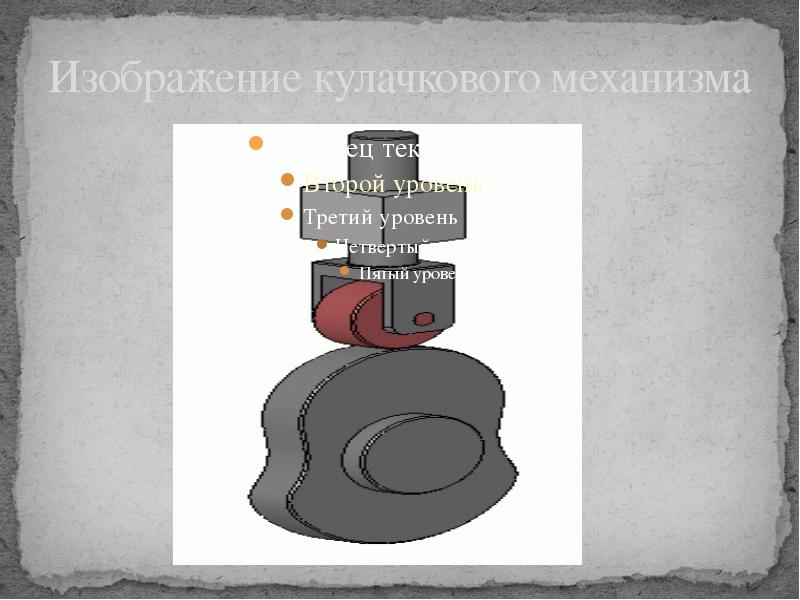
Вороты
Ворот простой - это древнейший механизм, состоящий из станка, в середине которого находится вал, который вертят посредством рычагов (вымбовки) и таким образом навивают на него веревку. С помощью этого ворота передвигают или поднимают разные тяжести.
Ворот сложный - это механизм, состоящий из станка с двумя желобоватыми чугунными валами, вращающимися в одно и тоже время, от вращения шестерни, приводимой в движение рычагами или вымбовками.
Ворот временный - это механизм, применяемый для вытягивания простых судов на берег и других тяжестей, состоит из круглого обрубка дерева, который ставится вертикально и удерживается в таком положении с помощью веревки или оттяжек, укрепляемых к стойкам, в некотором расстоянии от установленного обрубка, в землю вколоченного; к самому же обрубку или валу, привязывается рычаг, служащий для вращения.
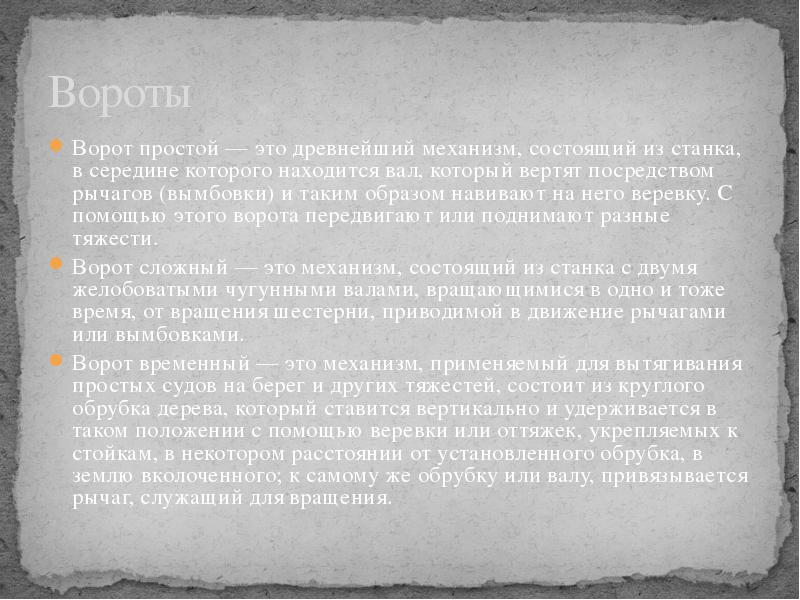
Изображение ворота
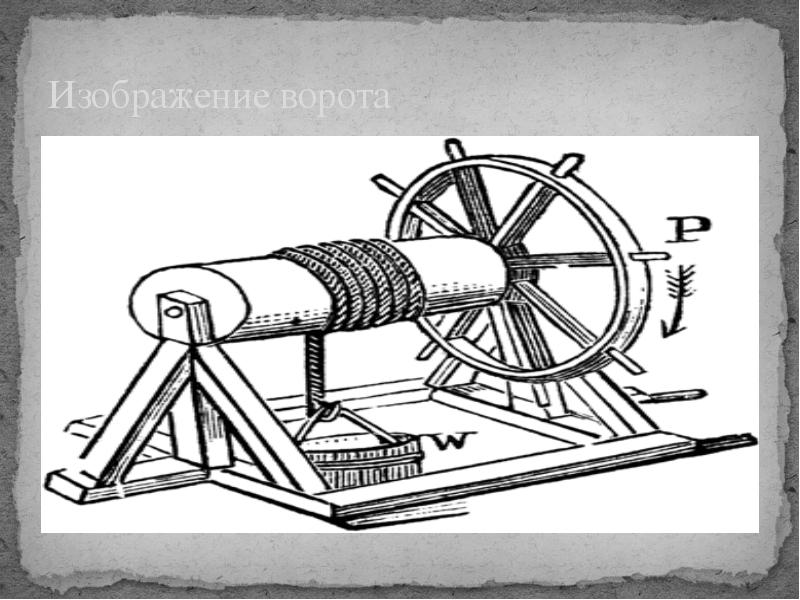
Блоки
Блок - простое механическое устройство, позволяющее регулировать силу, ось которого закреплена при подъеме грузов, не поднимается и не опускается. Представляет собой колесо с желобом по окружности, вращающееся вокруг своей оси.
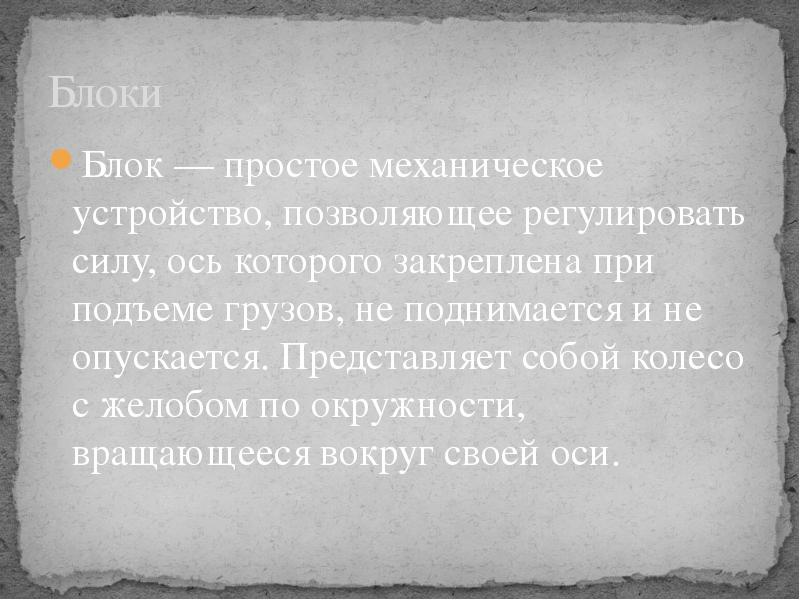
Неподвижный и подвижный блоки
Ось блока помещается в обоймах, прикреплённых на балке или стене, такой блок называется неподвижным; если же к этим обоймам прикрепляется груз, и блок вместе с ними может двигаться, то такой блок называется подвижным.
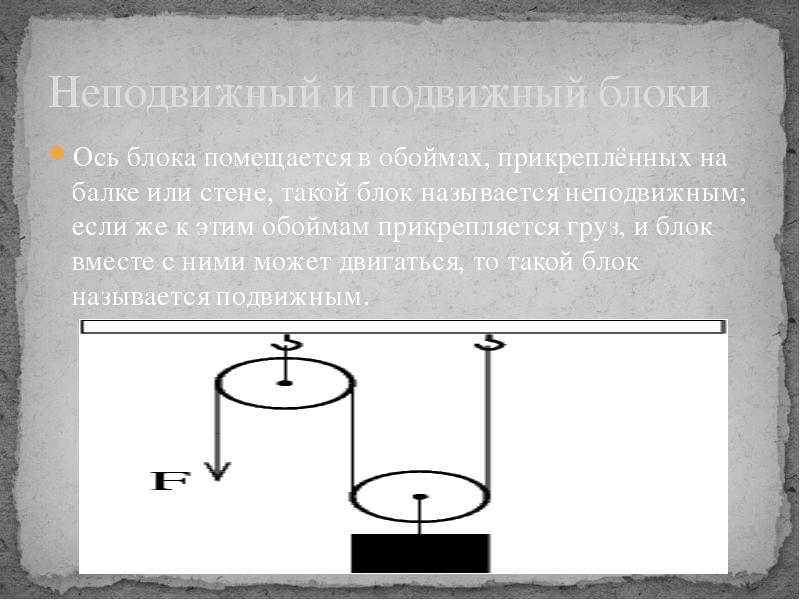
Реечная передача
Реечная передача - один из видов механических передач, преобразующий поступательное движение во вращательное. Может использоваться, например, в качестве механизма для передвижения объективной доски камеры или других приспособлений (теодолита, нивелира…) при наводке объектива на резкость, состоящий из ведущей шестерёнки и зубчатой рейки, по которым она перемещается.
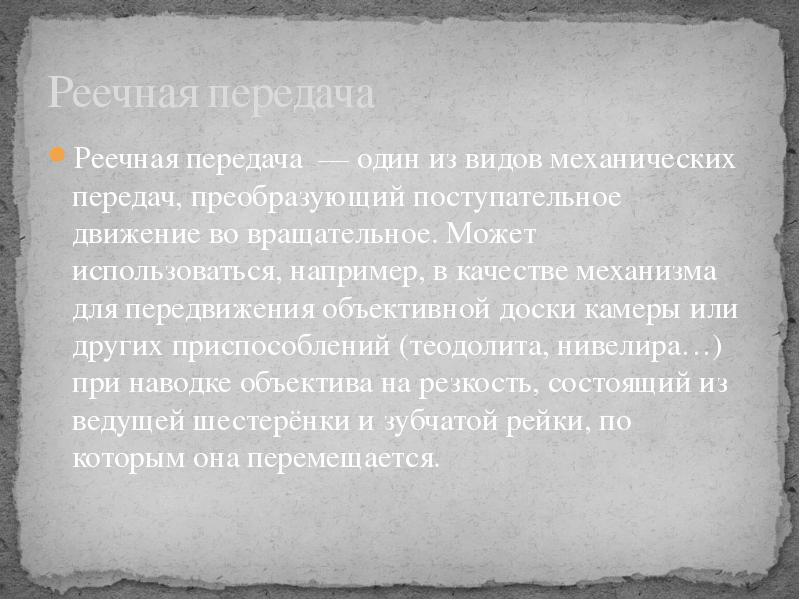
Изображение реечной передачи
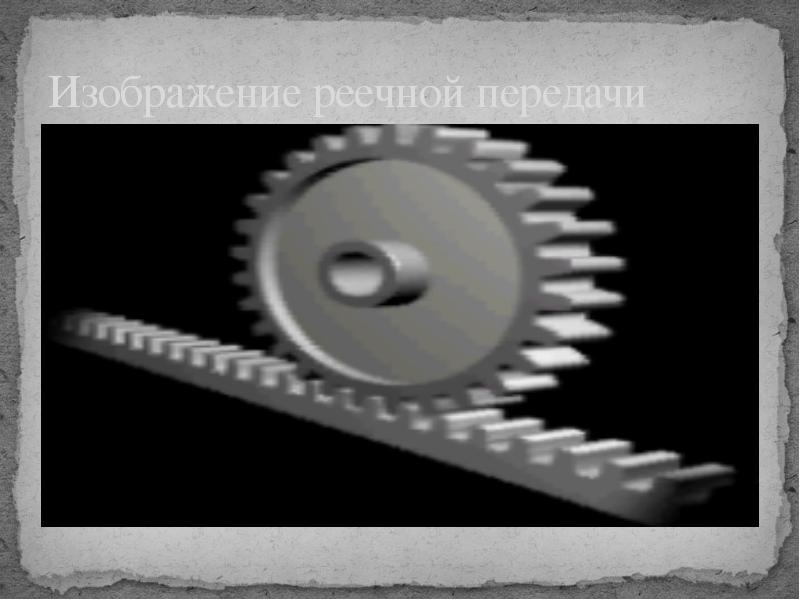
Кривошипно-шатунный механизм
Кривошипно-шатунный механизм (КШМ) предназначен для преобразования возвратно-поступательного движения поршня во вращательное движение (например, во вращательное движение коленчатого вала в двигателях внутреннего сгорания), и наоборот.
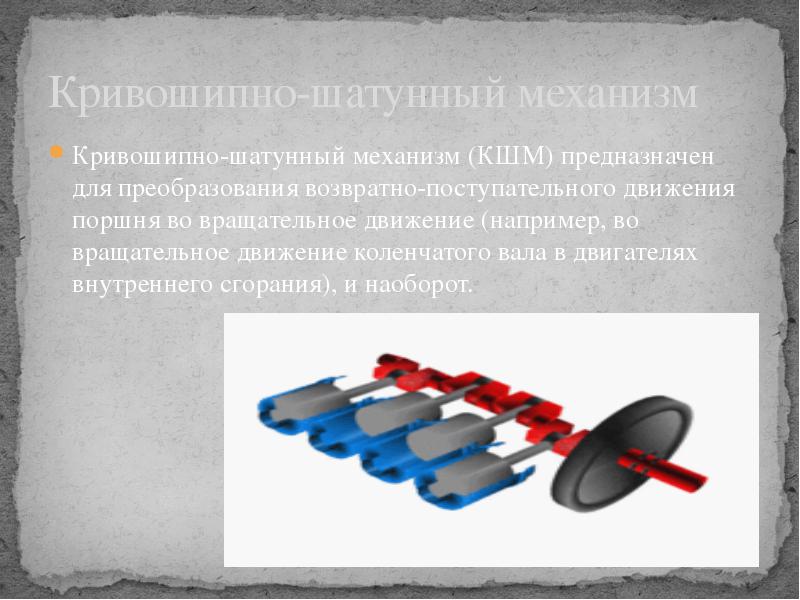
Наклонная плоскость
Плоскость, поставленная наклонно к горизонтальному направлению и употребляемая для поднятия тяжестей на высоту.
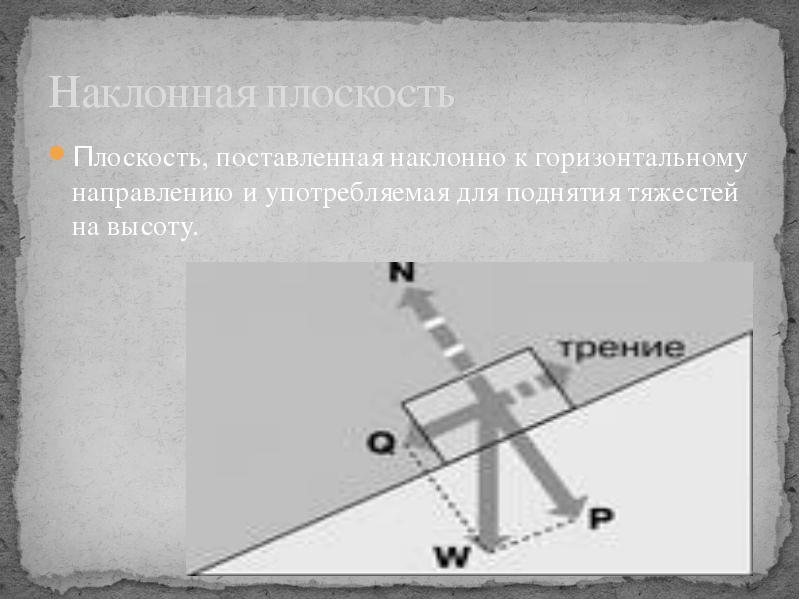
Расчетно-пояснительная записка к курсовой работе
«Технология изготовления рычага»
2. Выбор материала детали
4. Технологический процесс механической обработки «Рычага»
Использованная литература
1. Назначение и конструкция детали
Деталь «Рычаг» относится к деталям гидромашиностроения и входит в состав конструкции поворотно-лопастной гидротурбины типа турбины Каплана. Деталь «Рычаг» является составной частью механизма поворота лопастей рабочего колеса.
«Рычаг» представляет собой деталь, состоящую из плоской ступицы диаметром 980 с центральным отверстием диаметром 485 и отходящего от нее пальца с цилиндрическим галтельным основанием диаметром 250. Рычаг механизма поворота насаживается на цапфу лопасти (рис. 1 поз.3) посредством внутреннего отверстия диаметром 485 и скрепляется с цапфой лопасти 7 болтами М120х4. В конструкции предусматриваются также два цилиндрических штифта диаметром 130 для передачи крутящего момента от рычага к лопасти. Рычаг посредством пальца соединяется с серьгой (рис.1 поз.6), которая заменяет шатун, и шарнирно соединяется вторым своим концом с крестовиной. Крестовина через проушину и соединительные планки воздействует на рычаг, который, поворачиваясь, разворачивает лопасть рабочего колеса. Также «Рычаг» удерживает своей боковой поверхностью лопасть от осевого перемещения.
Рис. 1 Разрез рабочего колеса с дифференциальным поршнем: 1-дифференциальный поршень; 2-корпус р.к.; 3-лопасть; 4-цапфа; 5-РЫЧАГ; 6-серьга; 7- контршток сервомотора.
Для транспортировки и кантовки детали на его поверхности предусмотрено 3 отверстия под рым-болты М30.
2. Выбор материала детали
При работе турбины «Рычаг» подвержен большим нагрузкам: подвергается одновременному действию усилия, приложенному к его пальцу от сервомотора, и центробежной силы лопасти, цапфы и самого рычага, поэтому к его прочности предъявляются высокие требования. Для обеспечения необходимой прочности рычаг изготавливают из высокопрочных сталей путем ковки с последующей нормализацией 870-890 o C или закалкой 920-950 o C с отпуском 570-600 o C .
Исходя из вышесказанного, в качестве материала рычага принимаем конструкционную легированную сталь Сталь 30ГСЛ ГОСТ 977-88. Сталь применяется для деталей типа лопасти гидротурбин, рычаги, фланцы, сектора, венцы зубчатые, ролики обоймы, колеса ходовые и др., а также фасонные отливки, отливаемые методом точного литья, зубчатые колеса, бандажи, отливки небольших сечений и другие детали общего машиностроения к которым предъявляются требования повышенной твердости, сварно-литых конструкций с большим объемом сварки и др. Химический состав и механические свойства стали 30ГСЛ необходимо знать для выбора способа получения заготовки, режимов резания и технического нормирования.
Таблица 1. Химический состав стали 30ГСЛ ГОСТ 977-88
Таблица 2. Механические свойства
Таблица 3. Технологические свойства
Таблица 4. Общие сведения
Таблица 5. Литейные свойства
Материал детали обладает литейными свойствами и в то же время хорошо обрабатывается давлением, следовательно выбор процесса и метода изготовления заготовки связан с обеспечением данного качества детали, т.е. с техническими условиями на изготовление.
3. Выбор способа формообразования заготовки
Правильно выбрать заготовку - значит определить ее пригодность для изготовления детали с позиций прочностных и стойкостных характеристик, установить рациональный способ ее получения, определить оптимальные припуски на обработку ее поверхностей, рассчитать размеры заготовки и установить допуски на точность их выполнения, сконструировать заготовку и разработать оптимальные технические условия на изготовление.
Основными факторами, учитываемыми при выборе заготовки, являются:
масштаб и серийность выпуска (тип производства);
тип и конструкция детали (форма и размеры);
назначение детали в машине, материал и технические условия на изготовление;
планируемые сроки на технологическую подготовку производства;
конкретные условия производства (вооруженность завода и кадры);
экономичность заготовки, выбранной с учетом предыдущих факторов.
Все способы получения заготовок определяются:
1. Технологической характеристикой материала, т.е. его литейными свойствами или способностью претерпевать пластические деформации при обработке давлением, а такие структурными изменениями материала, получаемыми в результате применения того или иного метода выполнения заготовки (расположение волокон в прокате, поковках и штамповках, величина зерна в отливках и т.д.).
2. Конструктивными формами и размерами заготовки (например, чем крупнее деталь, тем дороже обходится изготовление штампа, модели или металлической формы).
3. Требуемой точностью выполнения заготовки и качеством поверхности.
4. Величиной программного задания (при больших партиях выгодны те способы изготовления заготовок, которые обеспечивают наибольшее приближение формы и размеров заготовки к форме и размерам готовой детали).
5. Производственными возможностями заготовительных цехов предприятия (наличием соответствующего оборудования).
6. Временем, затрачиваемым на технологическую подготовку производства заготовок (на изготовление штампов, моделей, прессформ, нестандартного оборудования и т.п.).
Выбор рациональной заготовки имеет важное экономическое значение для получения высоких технико-экономических характеристик заготовительных цехов и в целом для производства машин.
Рассмотрим несколько возможных способов формообразования заготовки детали «Рычаг» и примем наиболее рациональный из них.
Опытно-технологические разработки по изготовлению рычагов способами точного литья или сварки предварительно сформированных ковкой ступицы и пальца не позволили получить необходимую прочность рычагов для крупных гидротурбин. Поэтому примем к рассмотрению следующие способы:
Ковка с использованием подкладных штампов;
Отливка.
Способ изготовления рычага путем ковки с использованием подкладных штампов.
Рычаг представляет собой одну из самых ответственных и сложных по своей конфигурации деталей гидротурбины. Воспринимая усилие, необходимое для разворота лопасти и определяемое гидродинамическим моментом, рычаг одновременно подвержен воздействию знакопеременной нагрузки из-за пульсации потока. Для изготовления рычага выбирают материалы, обеспечивающие предел текучести 55-60 кгс/мм2 в сечениях 200-400 мм. Способ формообразования заготовок рычага должен обеспечивать высокую плотность и однородность материала, свободного от внутренних дефектов. При изготовлении поковок необходимо, чтобы ось заготовки приблизительно совпадала с осью слитка, а внешние очертания заготовки соответствовали наружным очертаниям рычага с учетом напусков и припусков на механическую обработку.
Эксцентричность выступа (пальца) по отношению к диску, имеющему расположенное в центре отверстие, создает ряд существенных трудностей при ковке рычагов. Технологический процесс изготовления поковок рычагов осуществляется за три нагрева под прессом с усилием 3000 тс (ковка заготовки) и прессом с усилием 10 000 тс (штамповка рычага). Для максимального приближения контура заготовки к контуру готовой детали заключительные операции формообразования выполняют на специальном штампе. После нагрева слитка до 1230° С проводятся закатка и обрубка излишка цапфы и биллетировка слитка, после второго нагрева - осадка слитка, требуемая для обеспечения необходимой плотности металла, протяжка и обжатие конца на конус. После обрубки заготовки в меру она загружается в печь. После третьего нагрева заготовку устанавливают выступом в отверстие штампа. Для лучшего заполнения штампа оттянутому конусному концу придается необходимый изгиб. Заготовку полностью осаживают верхней плитой, а разгонкой металла бойком добиваются сплошности заполнения полости штампа. После прошивки отверстия специальным прошивнем поковку выбивают из штампа и отправляют на термообработку.
Таблица 6. Схема изготовления поковки рычага
Операции и переходы | Эскизы переходов |
Первый нагрев (1230˚С) Закатка цапфы и обрубка ее излишка биллетировка слитка | ![]() |
Второй нагрев (1230˚С) | |
осадка слитка | ![]() |
подсечка | ![]() |
обжатие донного конца обрубка | ![]() |
Третий нагрев (1230˚С) | |
Оттяжка пальца | ![]() |
Осадка заготовки в штампе прошивка отверстия | ![]() |
Готовая поковка | ![]() |
Рис. 2 Эскиз кованой заготовки рычага
При описанном технологическом процессе коэффициент использования материала (по отношению к чистой массе) составляет: а) по черной массе - 0,5-0,65; 6) по слитку - 0,35-0,4. Для получения требуемого уровня механических свойств поковку подвергают термической обработке, режим которой устанавливается предприятием-поставщиком заготовки.
При этом изготовление сложных штампов под крупные заготовки также требует значительного расхода высокосортной стали, что также является существенным недостатком данного способа, учитывая низкую степень унификации рабочих колес гидротурбин.
В связи с высокой ответственностью рычагов их кованые за готовки относят к пятой группе испытаний, предполагающей индивидуальную приемку каждой поковки.
Изготовление рычагов свободной ковкой без использования подкладных штампов еще более затратно, т.к. в этом случае коэффициент использования металла не превышает 0,3.
Отливки получили широкое распространение во всех сферах и отраслях промышленности благодаря возможности получения деталей практически любой сложной геометрической формы из любых сплавов с внутренними полостями, что практически невозможно получить другими способами, как ковка, сварка. Отливки имеют большую степень конфигуративной точности и максимально приближены к деталям. Суммарная энергоемкость при изготовлении деталей из литых заготовок минимум в 2 раза меньше, чем при использовании других технологий.
Способ изготовления рычага литьем в песчаные формы
Распространенным способом производства литья является способ литья в песчаные формы (песчано-глинистые, жидкие самотвердеющие смеси (ЖСС), холоднотвердеющие смеси (ХТС) и др.). При этом способе в разовую подготовленную форму производится заливка жидкого металла. После затвердевания и охлаждения отливки форма разрушается. В зависимости от вида применяемых формовочных смесей и противопригарных красок обеспечивается различное качество отливок (по поверхности, внутренним дефектам, по отклонениям габаритных размеров и пр.). Несмотря на значительный расход формовочных материалов - до 3 т на 1 т отливок - данный способ наиболее распространен в литейном производстве, так как обеспечивает наибольшую универсальность и простоту формообразования. Наиболее всего данный процесс применим для индивидуального и мелкосерийного производства. Применяемые ЖСС и песчано-глинистые смеси обеспечивают хорошее качество отливок, получаемых из чугуна и стали.
Так как минимальный диаметр d отверстия, получаемого с помощью стержня, равен 6…10 мм при длине несквозного отверстия до 5d и сквозного отверстия до 10d, следовательно в отливке можно получить 2 отверстия расположенных на плоской ступице, что позволит повысить коэффициент использования металла и снизить количество механической обработки. Исходя из вышесказанного, отливка необходимой конфигурации получается с использованием 3 стержней.
Разработку технологического процесса изготовления отливки начинают с анализа технологичности конструкции детали.
Технологичной называют такую конструкцию изделия или составных ее элементов (деталей, узлов, механизмов), которая обеспечивает заданные эксплуатационные свойства продукции и позволяет при данной серийности изготовлять ее с наименьшими затратами. Технологичная конструкция характеризуется простой компоновки, совершенством форм. Конструкция отливки должна обеспечить удобство извлечения модели из формы, что достигается наименьшем количеством разъемов модели, отъемных частей и стержней.
Деталь «Рычаг» имеет конфигурацию средней сложности (2 группа сложности) и обладает достаточно хорошей технологичностью для изготовления ее способом литья. Минимальное и максимальное значение толщины стенок отливки равны соответственно 200 и 247,5 мм. Конфигурация и расположение поверхностей, подвергаемых обработке, полостей удовлетворяют основным требованиям литейной технологии. При изготовлении отливки целесообразно использовать прибыли, т.к. имеются тепловые узлы. Для выполнения полостей необходимо использовать стержни.
Определение размеров опок и выбор их из стандартного ряда.
Для отливки «Рычаг», габаритные размеры которой 1105х980х555 мм, экономичнее и целесообразнее взять опоку с габаритными размерами из стандартного ряда опок в соответствии с ГОСТ 2133-75:
Верхняя полуформа: 1400х1100х400 мм
Нижняя полуформа: 1400х1100х350 мм
Определение размерной точности отливки и величину припусков на механическую обработку производим в соответствии с требованиями ГОСТ 26645-85. Припуски на механическую обработку устанавливают в зависимости от допусков размеров отливок дифферецированно для каждого элемента. Для верхних частей отливки предусматривают больший припуск на механическую обработку так как там образуется неметалические включения.
1. Класс размерной точности отливки: Наибольший габаритный размер отливки 1105 мм. Тип сплава термообрабатываемая сталь. Технологический процесс- литьё в песчано-глинистые сырые формы из смесей с влажностью от 2,8 до 3,5% и прочностью от 120 до 160 кПа со средним уровнем уплотнения до твёрдости не ниже 80 единиц. Класс точности отливки 10
2.Допуски размеров отливки:
Таблица 7
3. Степень точности поверхности отливки:
Степень точности поверхности отливки 14
Рис. 3 Песчаная разовая форма в сборе: 1-верхняя полуформа, 2-литниковая система (литниковая чаша и стояк), 3- нижняя полуформа, 4-отливка, 5- стержень.
Рис. 4 Песчаная разовая форма в сборе (центральный стержень условно не показан): 6-стержни (образующие два отверстия по сечению Г-Г), 7- выпор, 8- вентиляционные отверстия.
Полуформы верхняя (поз. 1) и нижняя (поз.3) изготовлены из песчано-глинистой смеси в металлических рамках (опоках). В полуформах с помощью модели образована рабочая полость для получения отливки. Отверстия в отливке образуют песчаные стержни (поз. 5,6), которые прочно скреплены с формой с помощью стержневых знаков.
Полуформы перед заливкой скрепляют штырями. Для удаления газов, выделяющихся из песчано-глинистой смеси и расплава, при заливке в форме и стержне выполняют вентиляционные каналы (поз. 8). Расплав в рабочую полость формы заливают через литниковую систему (поз. 2) - совокупность каналов, предназначенных для подвода расплава в полость формы и питания отливки при затвердевании.
Назначение режимов термической обработки
Термическая обработка является обязательной операцией в технологическом процессе производства стального литья.
Цель термообработки заключается в том, чтобы путем нагрева до определенной температуры, некоторой выдержке при этой температуре и последующего охлаждения изменить структуру стальных отливок, и получить необходимые свойства прочности, пластичности, износоустойчивости, обрабатывающие или особые прочностные свойства.
ТО отливки детали «Рычаг»:
нормализация 870-890oC с отпуском 570-600oC .
При нормализации происходит полная фаза перекристаллизации, обеспечивая измельчение зерна, смягчение стали и снятие литейных напряжений: образуются структуры более тонкого перлита, чем при отжиге.
Отпуск заключается в нагреве ниже интервала превращений, выдержке при этой температуре и последующем охлаждении. При отпуске применяют превращение неустойчивых структур закалки в более устойчивые по схеме мартенсит-тростит-сорбит, и как следствие, с изменением структуры изменяются механические свойства, а также одновременно снимаются внутренние напряжения.
4. Технологический процесс механической обработки рычага
Особенность конструкции рычага обусловлена не только кинематикой механизма поворота, но и ограниченностью пространства в полости втулки рабочего колеса, что приводит к необходимости конструирования его в виде фасонной детали со скосами. При анализе ответственных сопряжений было установлено, насколько существенны перпендикулярность оси пальца к плоскости М и соблюдение (с точностью 0,2 - 0,3 мм) заданного расстояния между осями ступицы и пальца. Указанные требования обуславливают необходимость обеспечения технологического процесса специальной оснасткой. Ниже рассмотрены основные этапы технологического процесса механической обработки заготовки рычага, поставляемой в неободранном состоянии.
Рис. 5 Рычаг рабочего колеса
1. На разметочной плите производится расцентровка заготовки, разметка осей пальца и центрального отверстия. Размечаются поверхности К, Л, Р, М по высотным размерам h1, h2, L.
2. Деталь устанавливается на карусельном станке пальцем кверху и выверяется по его оси. Отрезается припуск для пробы, из которой изготавливаются образцы для испытания механических свойств. После испытания образцов выдается заключение о годности детали и возможности ее обработки.
3. Выполняется карусельная обработка рычага, для чего деталь устанавливают на подставки плоскостью М, совмещая ось пальца с осью вращения планшайбы карусельного станка. Базой для установки служат высотные и окружные риски разметки. Для исключения боя планшайбы из-за неуравновешенности массы рычага на планшайбе, в месте, противоположном ступице, укрепляют противовес. С припуском 5 мм подрезают торец пальца, точат поверхности d, Р и конусную поверхность, соосную с пальцем рычага. Деталь кантуют, устанавливают на проточенные кубари поверхностью Р и расцентровывают по риске разметки поверхности В. Растачивают центральное отверстие и подрезают плоскость М с припуском 5 мм.
4. Поверхность Н, необрабатываемая точением, фрезеруется на поворотном столе.
5. Рычаг вновь устанавливают на мерные подставки план шайбы карусельного станка пальцем вниз и выставляют по поверхностям М и В. Растачивают окончательно центровое отверстие по 2-му классу точности и подрезают торец. Для обеспечения необходимой шероховатости на участке Б поверхности М, контактирующем с торцом бронзовой втулки корпуса рабочего колеса, указанный участок обрабатывают шлифованием. После этого производят окончательную обработку пальца рычага.
Требуемая точность межосевого расстояния А обеспечивается технологически с помощью специального приспособления (рис. 6), на основании которого имеется центрирующая втулка 2 и съемный установочный штырь 3. Расстояние между осью штыря и втулки выдержано с точностью 0,1 мм. Приспособление устанавливают на планшайбу 4 карусельного станка и расцентровывают по цилиндрической поверхности штыря с помощью индикатора с точностью 0,02 мм. После закрепления приспособления на планшайбе штырь удаляют и рычаг устанавливают поверхностью В на центрирующую втулку и, разворачивая его относительно вертикальной оси, добиваются равномерного припуска по цилиндрической поверхности пальца.
Рис. 6 Приспособление для обработки пальца рычага
В этом случае погрешность размера А будет находиться в пре делах, определяемых соотношением
DА = Dпр + Dш + Dвт
где Dпр - погрешность межосевого расстояния А приспособления; Dш - несоосность установочного штыря с осью вращения планшайбы; Dвт - половина зазора в сопряжении центрирующей втулки с отверстием D рычага.
6. Рычаг устанавливают на разметочной плите вертикально, выверяя поверхность М (см. рис. 5.23) по угольнику таким образом, чтобы центры О и 0 находились в одной горизонтальной плоскости. Наносят базовую риску - ось положения пальца, перенося ее на поверхность М. С помощью зеркального кондуктора (того же, что использовался при разметке отверстий во фланцах лопасти и цапфы) размечают на поверхности М с выносом на образующую оси z и w. Размечают положение осей отверстий под болты и шпонки и дают риски обработки скосов по плоскости П.
7. На строгальном станке обрабатывают скосы одновременно для всего комплекта рычагов. детали выставляют по ходу стола и выверяют по рискам разметки.
8. На станке КУ-11 растачивают и нарезают отверстия под болты. Отверстия под шпонки растачивают с припуском 5 мм для совместной обработки с лопастью и цапфой.
9. Для увеличения прочности наиболее нагруженного сечения в месте перехода пальца рычага к диску производят наклеп галтели с помощью приспособления (рис. 5), надеваемого на палец рычага. Технология наклепа и оснастка разработаны ЦНИИТмашем. На корпусе 1 крепится пневматический молоток 2, устанавливаемый под углом 55˚ к оси пальца рычага. Ударный импульс передается ролику 3, радиус торовой поверхности которого равен 5 мм. В процессе наклепа приспособление проворачивается вокруг оси пальца, подвергая поверхностному пластическому деформированию галтель по всей окружности. Наклеп производится за два прохода при скорости вращения приспособления 1,5-2 об/мин. Частота импульсного воздействия ролика примерно 2000 ударов в минуту.
Оценка достигнутого уровня упрочнения осуществляется путем измерения деформации зоны галтельного перехода. Измерение проводится в направлении деформирующего усилия с по мощью индикатора, устанавливаемого в приспособление, конструкция которого аналогична описанному выше.
Рис. 7 Приспособление для наклепа галтели рычага
Использованная литература
1. Броновский Г.А, Гольдфарб А.И., Фасулати Р.К. Технология гидротурбиностроения Л:«Машиностроение», 1978 г.
2. ГОСТ 26645–85. Отливки из металлов и сплавов. Допуски размеров, массы и припуски на механическую обработку
3. Грановский С.А., Орго В.М. Конструкция и расчет гидротурбин
4. «Машиностроение», 1974г.
5. Ковалев Н. Н. Проектирование гидротурбин «Машиностроение», 1974г.
6. Михайлов А. М. и др. Литейное производство: Учебник для металлургических специальностей вузов. – М.: Машиностроение, 1987.
7. Орго В.М. Гидротурбины «Издательство Ленинградского университета, 1975 г.
8. Рихтер Р. Конструирование технологичных отливок. – М.: Машиностроение, 1968. – 254 с.
9. Шварцбурд Б.И. Технология производства гидравлических машин. - М: «Машиностроение»,1978 г.
К органам управления автомобилем относятся: рулевое управление и тормоза, вернее, вся тормозная система. Они являются главными органами и обеспечивают безопасность движения автомобиля. Поэтому к конструированию и изготовлению их нужно отнестись со всей серьезностью, чтобы достигнуть надежности, присущей современному транспортному средству, двигающемуся с большой скоростью в общем потоке автомобилей.
Рулевое управление
Рулевое управление должно обеспечивать движение автомобиля в соответствии с направлением, заданным водителем. Правильность движения управляемых колес не должна нарушаться ни при изменениях положения в результате подрессоривания, ни под действием неровностей и поперечного уклона дороги, бокового ветра, вменения коэффициента сцепления и сопротивления качению на колесах одной стороны по отношению к другим. Поворот рулевого колеса в любую сторону должен быть без значительного усилия и заеданий в рулевом механизме. Рулевое управление должно обеспечивать самовозвращение рулевого колеса из положения поворота в среднее положение.
Несоответствие кинематики рулевого привода и подвески (при деформации ее упругих элементов) также может вызвать колебание управляемых колес и ухудшить управляемость автомобиля. Чтобы избежать этого, рулевой механизм размещают на подрессорной части шасси и так располагают продольную рулевую тягу от сошки до переднего колеса, чтобы при любом движении колес она подвергалась наименьшим осевым перемещениям.
B современных автомобилях управляемыми колесами в подавляющем большинстве являются передние. Если два управляемых колеса размещены на одной оси, то, чтобы обеспечить раздельное поворачивание каждого колеса вокруг своего центра поворота (ряс. 47), их необходимо устанавливать на поворотных цапфах. Поворот передних управляемых колес на разные углы α и β должен обеспечивать их качение без скольжения по своим окружностям, описанным из центра поворота автомобиля. Чем круче поворот, тем больше разница между углами, на которые поворачиваются колеса.
Для обеспечения поворота управляемых колес на разные углы служит четырехзвенный механизм, называемый рулевой трапецией. У автомобилей, имеющих балку передней оси, рулевая трапеция образуется балкой передней оси, рычагами поворотных цапф и поперечной рулевой тягой. Такое рулевое управление называется нераздельным. В связи с распространенностью независимой подвески у передних управляемых колес в настоящее время применяется раздельный привод рулевого управления. Здесь рулевая трапеция образуется поперечиной кузова, рычагами поперечных тяг и составной поперечной тягой, соединенной с маятниковым рычагом.
При проектировании рулевого привода определяют размеры рычагов рулевой трапеции, углы их наклона по отношению к продольной оси автомобиля и подбирают необходимые передаточные числа рычажного привода к управляемым осям. Эти расчеты и последующую их проверку часто выполняют графически, вычерчивая в масштабе элементы рулевого управления (схематично) в плане и в виде сбоку. Чтобы проверить, выполняется ли необходимое соотношение между углами поворотов отдельных звеньев механизма, вычерчивают положение одного из элементов в нескольких позициях и связывают геометрически положение всех остальных звеньев.
Помимо выяснения правильности соотношения между углами поворота правого и левого колеса, при графической проверке следует убедиться в том, что перемещения рычагов подвески колес при наезде последних на неровности дороги не будут мешать перемещению рычагов рулевого привода и трапеции и наоборот. Поверочным графическим расчетом окончательно корректируют размеры элементов рулевой трапеции и привода, а также углов их наклона по отношению к продольной оси автомобиля.
При конструировании элементов трапеции можно воспользоваться простым, широко распространенным методом. В определенном масштабе вычерчивают прямоугольник, одна из сторон которого равна базе автомобиля L, а другая - расстоянию между осями поворотных цапф D (рис. 48). На продольной оси этого прямоугольника на расстоянии, равном 0,7 базы автомобиля, ставят точку С, которую затем соединяют прямыми линиями с точками, обозначающими оси поворотных цапф. Вдоль этих линий и располагают рулевые поворотные рычаги трапеции. Положение поперечной рулевой тяги и ее величину можно определить вначале расчетным путем, приняв отношение длины поворотных рычагов к длине поперечной рулевой тяги равным 0,12-0,14.
Затем графически, вычертив несколько положений трапеции, проверяют связь между углами поворота внутреннего и внешнего колес автомобиля. Если не учитывать увода колес, то оптимальным соотношением углов поворота управляемых колес будет такое, когда оси их вращения пересекаются на продолжении задней оси (рис. 47), что соответствует качению колес без бокового скольжения. При этом должно выполняться равенство
Для того чтобы учесть увод шин, возникающий из-за их эластичности, при построении трапеции следует брать не действительный размер базы автомобиля, а увеличенный на 25%
Но не только рулевая трапеция обеспечивает прямолинейное движение автомобиля при среднем расположении рулевого колеса. Во время движения на колеса действуют внешние силы, стремящиеся повернуть колеса вокруг шкворней. Если бы в сочленениях рулевого управления не было зазоров, тогда автомобиль "держал" бы дорогу, как это ему было задано рулевым колесом. Но при наличии зазоров под действием внешних сил колеса могут занять другое положение. Во избежание этого оси шкворней и сами колеса устанавливают с некоторым наклоном, чтобы при выводе колес из нейтрального положения они под действием возникающих сил сами возвращались в исходное положение. Это называется стабилизацией управляемых колес. Углы наклона колес к вертикали и горизонтали, направленной вдоль автомобиля, и углы отклонения шкворня от вертикали называются углами стабилизации передних колес автомобиля.
Угол развала колес у отечественных автомобилей находится в пределах 0° 30-1°. Сходимость колес можно принять около 3 мм, углы установки шкворней в поперечном направлении - 3-6°, в продольном - от 0° до 3°, Учитывая, что рулевое управление является важным узлом, обеспечивающим безопасность движения автомобиля, необходимо, особенно при создании четырехместных микроавтомобилей, использовать уже имеющиеся заводские конструкции и только в исключительных случаях применять самодельные рулевые управления. Это, конечно, не относится к тихоходным и небольшим по весу детским микроавтомобилям. Здесь конструктор может в полную меру приложить свои знания и, возможно, создаст оригинальное рулевое управление, не уступающее заводским конструкциям.
Во всех остальных случаях, если возникнет необходимость, рулевые управления следует делать по подобию тех, которые установлены на мотоколясках и автомобилях "Москвич" и "Запорожец", с максимальным использованием деталей от этих механизмов, особенно шарнирных сочленений рулевых тяг. Детали и узлы их можно приобрести в автомагазинах и магазинах спортивных товаров. При конструировании рулевых управлений следуй правильно подобрать передаточное отношение как рулевого механизма, так и рулевого привода. Исходить нужно из максимальных углов поворота управляемых колес, которые не должны превышать 40-45°, при этом рулевое колесо у автомобилей делает поворот на 1,5-3 оборота в каждую сторону, что соответствует угловому передаточному числу, равному 12÷25. Угловые же передаточные числа рулевых механизмов автомобилей "Москвич" и "Запорожец" равны 17, а мотоколяски - 10,5. Угловое передаточное число рулевого управления i ω , представляющее отношение угла поворота рулевого колена к углу поворота управляемых колес, есть произведение передаточного числа рулевого механизма i м и рулевого привода i п
Под угловым передаточным числом рулевого механизма понимают отношение угла поворота колеса и вала сошки или соответственно угловые скорости вращения рулевого колеса и вала сошки
где dθ к, dθ с - элементарные углы поворота рулевого колеса и вала сошки;
ω к, ω с - соответственно их угловые скорости. Передаточное число рулевого привода i п зависит от соотношения плеч рычагов привода и может быть определено как отношение плеч рычага поворотной цапфы и рулевой сошки
Если имеется готовый рулевой механизм, но с недостаточным угловым передаточным числом, то можно несколько повысить общее угловое передаточное число рулевого управления, подбирая соответствующие длины рычага поворотной цапфы и рулевой сошки. В случае отсутствия рулевого механизма можно самому изготовить его. Для этого нужно использовать простой механизм типа шестерни-рейки, который позволит сократить в рулевом приводе количество шаровых соединений, являющихся ответственными узлами привода, Однако этому механизму присущи некоторые недостатки. Его угловое передаточное отношение, о котором говорилось выше, редко превышает 10-12. При разработке конструкции механизмов такого типа трудно получить удовлетворительный узел компенсации неравномерного износа рейки. Он не создает у водителя ощущения движения по прямой.
В механизмах других типов передаточное отношение изменяется с изменением угла поворота рулевого колеса. Несколько изменяется также коэффициент полезного действия механизма. Это позволяет водителю, как говорят, чувствовать то положение рулевого колёса, при котором автомобиль движется прямолинейно. Этот недостаток реечного рулевого механизма можно устранить, если фиксировать среднее положение рейки, соответствующее движению колес по прямой, с помощью шарикового фиксатора.
На рис. 49 показана простейшая конструкция рулевого механизма реечного типа. Рулевой вал 1 с помощью штифтов или другого элемента соединяется с хвостовиком шестерни 11, располагаемой в картере рулевого механизма 4. Хвостовик шестерни вращается во втулке 3, зажатой между крышкой картера 2 и упорной шайбой 12. Положение шестерни вдоль ее оси изменяется с помощью регулировочного винта 8. Рейка 7 перемещается перпендикулярно оси шестерни в специальном направляющем отверстии картера рулевого механизма.
Рейка с одного конца закрыта глухим резиновым чехлом 5, а с другого защищена от попадания грязи и влаги в механизм гофрированным резиновым чехлом 9. Выступающий из гофрированного чехла конец рейки имеет два конических отверстия, в которые укрепляют шаровые пальцы шарниров поперечных тяг, так как этот механизм предназначен для независимой подвески передних управляемых колес. Он может применяться и для управляемых колес с неразрезной балкой и зависимой подвеской, тогда будет вполне достаточно одного отверстия. На литом картере имеются две проушины 6 для крепления рулевого механизма к балке передней подвески. При самостоятельном изготовлении рулевого механизма картер можно выполнить сварным из выточенных на токарном станке деталей. От проворачивания во время работы механизма рейка удерживается шпонкой, помещенной в нижней части картера. Шпонка крепится на винтах, и под нее ставят прокладки. Изменяя толщину прокладки под шпонкой, можно устранить зазор между шестерней и рейкой. Расстояние между шестерней и рейкой можно изменить и за счет поворота эксцентриковой втулки.
Те, кто знаком с расчетом деталей на прочность, могут не только подобрать узлы и элементы рулевого управления, но и произвести проверочные расчеты всех рычагов и тяг. Нагрузки на детали рулевого управления подсчитывают, когда известно усилие, приложенное к рулевому и управляемым колесам.
В первом случае считается, что водитель на окружности рулевого колеса может приложить касательную окружную силу, равную 40 кгс. Тогда нетрудно подсчитать момент, соответствующий этой силе, который будет приложен к валу рулевого колеса,
Затем нетрудно определить нагрузки во всех звеньях рулевого управления, рассматривая последовательно кинематическую связь его отдельных элементов. Коэффициент полезного действия рулевых механизмов колеблется в пределах от 0,5 (червячных) до 0,8 (механизмов реечного типа). Общий к. п. д. рулевого управления для автомобилей с одной передней управляемой осью составляет 0,5-0,7.
Во втором случае за расчетный принимается момент сопротивления повороту колес на месте. Для расчетов можно воспользоваться полуэмпирической формулой, которая дает результаты, достаточно близкие к действительным,
φ - коэффициент сцепления;
Р - давление воздуха в шине.
где l с - плечо рулевой сошки;
l п.р. - плечо поворотного рычага;
R к - радиус рулевого колеса;
i п - передаточное число рулевого механизма;
η р.у. - к. п. д. рулевого управления.
Так как рулевой механизм в самодельных микроавтомобилях берется из готовых, изготовляемых заводами на его расчете останавливаться нет надобности. Чаще всего приходится либо изготавливать, либо подгонять из существующих вал рулевого управления. Рассчитывав вал рулевого управления на прочность, следует определить возникающие в нем напряжения от кручения по формуле
где М в - момент на валу, кгм;
D - наружный диаметр полого вала, м;
α - отношение внутреннего диаметра вала к наружному
Полученное напряжение при сдвиге сравнивают с допускаемым напряжением, которое следует брать по пределу текучести, принимая запас прочности n в пределах 2,5-3,5.
где σ т - предел текучести для данного материала, кгс/м 2 . Если вал длинный, тогда необходимо произвести расчет на жесткость, определяя угол закручивания по формуле
где l в - длина вала, м;
М к - максимальный крутящий момент на валу, кгс/м 2 ;
G - модуль сдвига, который в расчете стальных деталей следует принимать равным 78-80 кгс/м 2 ;
J - полярный момент инерции сечения, м 4 .
Полярный момент инерции вала сплошного сечения подсчитывается так
а для полого вала при известном отношении
Рычаги, работающие на изгиб и кручение (сошка, рычаги, передаточные рычаги поворотных цапф), рассчитываются на сложные напряжения изгиба и кручения по известным формулам сопротивления материала. Продольная, поперечная межосевые тяги привода рассчитаются на сжатие и продольный изгиб. Растяжение вызывает меньше опасений. Сжатие тяг может привести к потере их продольной устойчивости. Поэтому следует произвести расчет на определение критического напряжения, при котором появляется опасность потери устойчивости. Это можно сделать по формуле
где l - длина тяги;
F - площадь поперечного сечения тяги, м 2 ;
Е - модуль упругости первого рода, кгс/м 2 ; *
* (Модуль упругости для стальных деталей в расчете можно принимать равным 200÷210 кг/м 2 . )
I - экваториальный момент инерции сечения, который для круглого сечения подсчитывается по формуле
После чего рассчитывается напряжение сжатия по формуле
где Р т - продольное усилие, кгс.
Зная критическое напряжение и напряжение сжатия, можно определить запас устойчивости, который представляет собой отношение критического напряжения к напряжению сжатия
Запас устойчивости следует принимать равным 1,25-2,5. При изготовлении рулевого механизма для шестерни следует брать цементуемую сталь 12ХНЗА. Рейку можно изготавливать из углеродистой стали 45 с последующей термообработкой (закалкой и отпуском). Для рулевых валов и рулевых тяг применяются бесшовные трубы из стали 30, 35 и 40. Рычаги поворотных цапф и сошек рекомендуется делать из стали 40, 40Х и 40ХН.
Тормозная система
Другой системой, от которой также зависит безопасность движения, является тормозная система. Состоит она из тормозов, которые располагаются обычно на колесах, и тормозного привода, передающего усилие от рычага или педали к тормозным механизмам.
По существующим в Советском Союзе нормативам тормозной путь легковых автомобилей при торможении на горизонтальном участке дороги со скорости 30 км/час должен быть не больше 7,2 м, а максимальное замедление при этом не менее 5,8 м/сек 2 .
Если рассматривать процесс торможения, то за все время тормозного пути действительное торможение с полным тормозным моментом на колесах происходит только за определенную часть этого пути. Какое-то, хотя и небольшое, время необходимо для реакции водителя и срабатывания тормозного привода, куда относятся выбор зазора в приводе и механизме тормозов и нарастание тормозного усилия. Учитывая последнее, можно сразу сказать, что гидравлический привод в тормозных системах предпочтительней, так как время срабатывания у него является наименьшим. Но все же в самодельных микроавтомобилях, а также в мотоциклах применяется большей частью механический привод как наиболее простой в изготовлении.
Для безопасности и безотказности действия тормозов на автомобилях устанавливают две или даже три тормозные системы. В микролитражных машинах в основном две системы тормозов: рабочий и стояночный тормоз. У автомобилей с весом не выше 600 кг допускается установка рабочих тормозов только на задние колеса, в то время как на автомобилях с большим весом тормоза должны быть на всех колесах.
Если на микроавтомобиле вы решили использовать гидравлическую систему привода тормозов, то, конечно, ее лучше всего взять от автомобиля "Запорожец" или от мотоколяски СЗАМ, для чего на колесах нужно установить тормозные диски и тормозные барабаны вместе с внутренними механизмами. Эти системы подробно описаны в специальной технической литературе.
Все же большее распространение на самодельных микроавтомобилях, как уже отмечалось выше, получают тормоза с механическим приводом. Они более просты в устройстве и эксплуатации, несмотря на то, что время срабатывания привода несколько больше и сложнее их регулировка. На рис. 50 показано устройство механического привода тормозов, которое может быть применено на микролитражных автомобилях. Тормозная педаль 5, укрепленная на валике 9, с помощью рычагов и тросов воздействует на рычаги разжимного кулака 7 и через них на тормозные колодки. На этом же валу находится привод ручного тормоза, связанный с рычагом 4, который при действии ножного тормоза остается на месте.
Если происходит затормаживание ручным тормозом, педаль не изменяет своего положения, так как свободно сидит на валу и поворачивает последний, действуя на специальный упор. Таким образом, в данной конструкции рабочие тормоза всех четырех колес являются стояночными. Привод ручного тормоза можно сделать только на два задних колеса. Рычаг привода ручного тормоза должен обязательно иметь фиксирующее устройство, для того чтобы его можно было оставлять в заторможенном состоянии. Обычно это устройство выполняется в виде храпового механизма, Чтобы обеспечить одинаковые усилия в приводе на каждое из задних колес, в механизм привода включается уравнительное устройство. За счет различной длины рычагов привода, насаженных на вал, можно изменять тормозные усилия передних и задних колес. В механизме привода тормозов обязательно должны быть предусмотрены регулирующие устройства натяжения тросов для регулировки свободного хода педали и рычага стояночного тормоза. Проектируя привод, следует тщательно продумать все узлы, чтобы исключить возможность заеданий механизма в процессе эксплуатации.
Тормозные устройства колес для системы с механическим приводом необходимо брать готовые, заводские, которые устанавливаются на мотоциклах, мотороллерах и мотоколясках.
При выборе тормозных устройств необходимо обратить внимание на те, которые будут наиболее эффективными для автомобиля данного веса, т. е. они должны развивать на колесах требуемые тормозные усилия. Если тормоза недостаточно мощные, возрастет тормозной путь автомобиля. Если же тормозной момент у выбранного тормоза больше, чем требуется, будет происходить частая блокировка колес при торможении. Это приводит к повышенному износу шин и к возрастанию тормозного пути. Исследования показали, что тормозной путь автомобиля с заблокированными колесами на 15-20% больше, чем при торможении, когда колеса находятся на грани блокировки.
Тормозные усилия на колесах и тормозной момент, которые потребуются автомобилю, можно подсчитать после завершения компоновки, когда ориентировочно будет известен полный сухой вес автомобиля. Нужно узнать вес автомобиля с пассажирами и снаряжением. Зная процентное распределение веса по осям, можно подсчитать нагрузку на каждое колесо.
При этом следует учитывать перераспределение нагрузок по колесам в процессе торможения. Нагрузка на передние колеса возрастет, а на задние - уменьшится. Когда известны статические нагрузки на колеса G п и G з, высота центра тяжести h, расстояние центра тяжести по горизонтали от передней оси а, можно подсчитать возникающие реакции на колесах передней и задней оси.
Для колес передней оси
Для колес задней оси
Если положение центра тяжести автомобиля неизвестно, тогда ориентировочно можно определить перераспределение нагрузки по осям, умножая статические нагрузки на коэффициенты перераспределения, которые для передней оси можно взять в пределах m 1 =1,7, а для задней оси m 2 =0,6 (значения средние). Тогда
Зная нагрузки, приходящиеся на каждое колесо, можно подсчитать тормозное усилие, которое необходимо приложить к колесу, чтобы полностью использовать его сцепной вес на дороге с твердым покрытием. Для этого в расчете принимаем коэффициент сцепления 0,8 (значение для обычных асфальтовых дорог). Перемножив вес, приходящийся на колесо, на этот коэффициент, получим максимально возможное тормозное усилие, которое допустимо по сцеплению колеса с дорогой
Если теперь это тормозное усилие умножить на радиус качения колеса, получим максимальный тормозной момент, который можно допустить на колесе при полном использовании сцепного веса. Тормозной момент больше этого расчетного приведет к блокировке колес со всеми нежелательными явлениями, о которых говорилось выше.
Когда тормозные механизмы на всех колесах будут одинаковыми, их следует подбирать по наиболее нагруженному колесу (максимальному тормозному моменту). Зная конструкцию тормоза, можно определить значение тормозного момента аналитически - расчетным путем. Расчет тормозных механизмов различных типов приведен в специальной литературе * .
* (А. С. Литвинов, Р. М. Ротенберг, А. К. Фрумкин. Шасси автомобиля. Конструкция и элементы расчета. М., Машгиз, 1963.
Н. А. Бухарин, В. С. Прозоров, М. М. Щукин. Автомобили. Теория рабочих процессов, теория прочности агрегатов и систем автомобиля (под ред. Н. А. Бухарина). М., "Машиностроение", 1965.)
Подобрать тормозные механизмы можно другим методом, не производя расчета. Известно, что тормоза мотоциклов, мотороллеров и мотоколясок обеспечивают при установленной нагрузке необходимую эффективность торможения. Следовательно, если определить нагрузку на колеса и принять условия, аналогичные вышерассмотренным (когда коэффициент сцепления 0,8), нетрудно подсчитать тормозное усилие и тормозной момент.
Наконец, имея собранный тормозной механизм, можно чисто экспериментальным путем определить тормозной момент следующим образом. Закрепить колесный тормоз за опорный диск (рис. 51). На тормозной барабан установить рычаг, длина которого должна быть несколько больше 1 м, чтобы затем на нем, на расстоянии 1 м от центра оси тормозного барабана, можно было сделать отметку или треугольный запил. При заторможенных колодках на расстоянии 1 м на рычаг навесить гири или навески, пока барабан не провернется. Вес гирь укажет в данном случае тот тормозной момент, который могут дать испытываемые тормоза. При этом необходимо, чтобы усилие на рычаге тормозного кулачка, разжимающего колодки, было такое же, какое возникает в результате нажатия на педаль с силой 50 кг. Определить это усилие можно тогда, когда в тормозном приводе известны плечи всех рычагов привода и выбрана педаль. Конечно, лучше всего определять требуемый тормозной момент, укрепляя тормозные механизмы с рычагом на ступицах колес собранного шасси с готовым тормозным приводом.
При длительном торможении тормозные колодки нагреваются, и в результате снижения коэффициента трения между поверхностями тормозных накладок и барабаном начинает снижаться эффективность торможения. Поэтому, конструируя тормозные механизмы, необходимо произвести расчет нагрева тормозов. Учитывая сложность и недостаточную точность такого расчета, эффективность действия тормозов при длительном торможении часто определяют отношением веса автомобиля к общей площади тормозных накладок
В легковых автомобилях, у которых тормоза находятся в худших условиях для охлаждения, так как колеса располагаются под крылом кузова и эффективность торможения выше ввиду высоких скоростей и больших замедлений, рекомендуется брать это отношение в пределах 1,3÷4,0 кгс/см 2 .
Ручной стояночный тормоз, предназначенный для удержания автомобиля на наибольшем подъеме, должен быть достаточно эффективным. Наиболее неблагоприятными условиями для автомобиля, имеющего привод от стояночного тормоза только на задние колеса, будут такие, когда он не затормаживается на уклоне. В этом случае для удержания его потребуются тормоза, способные развивать тормозной момент, равный:
где α - величина уклона в градусах;
L - база автомобиля, м;
h - высота центра тяжести, м;
а - расстояние по горизонтали от передней оси до центра тяжести, м;
r к - радиус качения колеса, м;
G a - полный вес (масса) автомобиля, кг.
При затормаживании автомобиля на подъеме с величиной угла подъема α на задних его колесах должен быть приложен несколько больший момент, чем рассчитанный по вышеприведенному уравнению. В этом случае необходимо, чтобы тормоза развивали тормозной момент, равный
Описанное выше относится к приводу стояночного тормоза только на задние колеса. Когда же стояночный тормоз при затормаживании автомобиля действует на все колеса, то общий тормозной момент должен быть равен
При известных значениях тормозных моментов на колесах, используя вышеприведенные уравнения, можно решить обратную задачу по определению максимального угла наклона, на котором эти тормоза еще будут способны удерживать автомобиль.
Рычаг привода стояночного тормоза должен быть так связан с остальными деталями тормозных механизмов, чтобы водитель, затормаживая автомобиль, перемещал его по направлению к себе.
Ходовая часть
Конструируя ходовую часть шасси, соединять раму или кузов с мостами (колесами) автомобиля следует элементами подвески, в которую входят упругие элементы, направляющие устройства и амортизаторы.
Первые смягчают динамические нагрузки, действующие от колес на раму, и обеспечивают требуемую плавность хода.
Направляющие устройства передают на раму действующие со стороны Дороги и колеса силы и моменты, а амортизаторы предназначены для гашения возникающих колебаний.
В качестве упругих элементов подвески применяются листовые рессоры, спиральные пружины, торсионы, резиновые и телескопические гидравлические элементы. Пневматические элементы, получающие в последнее время распространение в автостроении, при создании самодельных автомобилей пока не используются.
Колебания подвески гасятся большей частью гидравлическими амортизаторами одностороннего и двустороннего действия, которые выпускаются промышленностью, а иногда за счет трения в упругом элементе и направляющем устройстве или за счет специально сконструированных амортизаторов механического трения.
В самодельных микроавтомобилях могут применяться как зависимые подвески, когда перемещение одного колеса в поперечной плоскости передается другому колесу, так и независимые, при которых непосредственная связь одного колеса с другим отсутствует. В зависимых подвесках правое и левое колеса одной оси связываются жесткой балкой, которая через подвеску связана с рамой или кузовом автомобиля. В независимых подвесках каждое колесо связывается с рамой или кузовом одним или двумя рычагами, перемещающимися независимо друг от друга.
На рис. 52 приведены основные типы независимых подвесок, которые могут быть использованы для самодельных микролитражных автомобилей. Первые две схемы (а и б) дают представление об однорычажной и двухрычажной подвесках с перемещением колес в поперечной плоскости. Две другие схемы (в и г) показывают, как можно выполнить однорычажную и двухрычажную подвески колес, качающихся в продольной плоскости. Если ось крепления рычага разместить под углом к продольной оси автомобиля, то можно получить подвеску с перемещением колес одновременно в продольной и поперечной плоскостях (рис. 52, д). Наконец, встречается вариант свечной подвески (рис. 52, е), когда колесо при наезде на препятствие поднимается вертикально вверх, не изменяя углов установки.
Для зависимых подвесок наиболее простой является подвеска на полуэллиптических рессорах (рис. 53). Такие рессоры, например, применены в автомобилях "Юный сибиряк" и "ХАДИ-2". Рессора является не только упругим элементом, но и составляющей частью направляющего устройства. За счет трения между рессорными листами происходит частичное гашение возникающих колебаний. Но все же и при этой подвеске для обеспечения комфортабельности часто необходимо ставить амортизирующие устройства. Вместо рессор в качестве упругого элемента в зависимых подвесках могут употребляться винтовые пружины с расположенным внутри или снаружи их резиновым буфером. Подвеска на пружинных упругих элементах обязательно требует направляющего устройства для передачи продольной силы и ее моментов. Пружинные упругие элементы, так же как и торсионные, не обладают способностью гасить возникающие колебания, а поэтому при применении их обязательно наличие амортизирующих устройств.
На рис. 54 показан один из возможных вариантов зависимой подвески с упругими элементами в виде спиральных пружин. Применять зависимую подвеску обычно рекомендуется для неуправляемых колес. А на микролитражных автомобилях из-за расположения силового агрегата в задней части автомобиля, даже для задних неуправляемых колес, применяют большей частью независимую подвеску. Это позволяет более компактно разместить силовой агрегат и главную передачу, а также снизить общую высоту автомобиля. Примером такой конструкции может служить независимая подвеска ведущих колес автомобиля БМВ-700, относящаяся к типу однорычажных с качением колеса в продольной плоскости. Направляющим элементом здесь является рычаг, прикрепленный к раме шарнирно в двух точках.
На следующем рис. 55 изображена однорычажная независимая подвеска колеса, где в качестве упругого элемента применен пластинчатый торсион, заключенный в трубчатый чехол, который одновременно является поперечиной рамы. Такая подвеска проста в изготовлении и может с успехом применяться в конструкции самодельных автомобилей. Рычажные подвески с качением в продольной плоскости, помимо простоты, обеспечивают при колебании колес постоянство колеи.
Недостатками однорычажных подвесок с продольным расположением рычагов являются значительный наклон шин при повороте и трудность в обеспечении необходимой жесткости рычага при действии боковых сил и моментов.
Это можно устранить, если ось качения рычагов однорычажной подвески расположить под углом к продольной оси автомобиля, т. е. изготовить подвеску по схеме, изображенной на рис. 52, д. Тогда колеса смогут перемещаться как в продольной, так и в поперечной плоскостях. Подобное направляющее устройство в виде вильчатого качающегося рычага с резиновыми втулками в качестве шарниров применено в задней подвеске автомобиля "Запорожец".
Описание других типов подвески колес существующих микролитражных автомобилей можно найти в специальной литературе.
В самодельных микроавтомобилях очень широко используется подвеска от мотоколясок Серпуховского завода. Передний мост этих колясок имеет независимую торсионную подвеску. Подвеска задних колес независимая с цилиндрическими пружинами. В качестве упругих элементов внутри пружины вставлен резиновый буфер, ограничивающий сжатие витков.
Фрикционный амортизатор задней подвески мотоколясок (рис. 56) состоит из двух внутренних 3 и двух наружных 7 пластин, двух фрикционных шайб 4, выпуклой стальной шайбы 5, пружинной шайбы 2, стяжного болта 6 с гайкой 1 и стопорного кольца 9. Внутренние и наружные пластины одним концом своим насажены на стальную втулку и соединены с ней сваркой. Другие концы внутренних и наружных пластин через фрикционные шайбы соединены между собой посредством стяжного болта, выпуклой шайбы и гайки. Это дает возможность внутренним и наружным пластинам проворачиваться относительно друг друга. Изменять жесткость амортизатора можно, завертывая или ослабляя гайку стяжного болта.
В качестве независимой подвески задних колес можно использовать маятниковую вилку мотоциклов Ижевского завода вместе с амортизирующими устройствами, которые одновременно являются и упругими элементами подвески. Для маленьких двухместных машин следует брать подвеску легких мотоциклов, а для больших - подвеску тяжелых мотоциклов. Можно использовать отдельные элементы торсионной подвески коляски мотоциклов М-61 и М-62.
На небольших автомобилях с приводом на одно колесо можно установить подвеску заднего колеса мотороллера ВП-150, у которого силовой агрегат размещен на качающемся рычаге подвески. Заднюю подвеску мотороллера Т-200 можно применить при изготовлении однорычажной независимой подвески с качением рычага в продольной плоскости. Здесь в качестве направляющего устройства будет служить качающаяся вилка, а пружинно-гидравлический амортизатор является одновременно и упругим элементом и узлом, гасящим возникающие колебания.
В автомобилях, у которых вес на заднюю ось будет не более 300 кг, можно ставить подвеску задних колес грузовых мотороллеров МГ-150 и ТГ-200. Упругим элементом подвески мотороллера МГ-150 служат торсионные валы, а возникающие колебания гасятся фрикционными амортизаторами. Независимая же подвеска задних колес мотороллера ТГ-200 пружинного типа состоит из трапециевидных рычагов и спиральных пружин с резиновыми буферами. С каждого конца пружины установлены металлические чашки, служащие для соединения концов пружин с полуосью и рамой.
Расчет подвески автомобиля представляет собой трудную инженерную задачу, которая зачастую решается с помощью электронно-вычислительных машин. Тем не менее в практике выработались некоторые критерии, по которым можно судить в какой-то мере о подвеске построенного автомобиля. По опыту изготовленных конструкций можно сказать, что удовлетворительная плавность хода легковых автомобилей может быть получена, если эффективный прогиб подвески под действием статической нагрузки будет лежать в пределах 150-300 мм при независимой подвеске колес и 80-140 мм при зависимой подвеске колес. Причем, по данным испытаний, у лучших по плавности хода автомобилей передняя подвеска обычно мягче задней.
Самодельные автомобили для малышей, имеющие небольшие скорости движения, можно делать без упругих элементов подвески, так как эластичность шин вполне достаточна для создания необходимой комфортабельности езды на таком автомобиле. Тем более, что используются они в основном на дорожках парка или двора, где поверхность обычно гладкая.